Aumento da produtividade com um passo duplo na máquina aerossol
Cada vez é maior a demanda de produção dos aerossóis, portanto, as empresas fabricantes têm que otimizar seus métodos para obter excelentes resultados. Existem vários procedimentos para aumentar essas demandas. Um deles é o Aumento da Produtividade com um passo duplo na Máquina de Aerossol, tema ministrado no passado Seminário Técnico do Aerossol e que hoje publicamos integralmente.
ÍNDICE
1. ¿O que é um passo duplo?
2. Ciclo de Vida
3. Sistema de produção
4. Identificação da necessidade
5. Objetivo
6. Situação atual do equipamento
7. Alternativa
8. Desenho
9. Execução
10. Implementação da melhoria
11. Avaliação
12. Resultados Obtidos
13. Tempo de retorno da inversão
14. Conclusões
1. ¿O QUE É UM PASSO DUPLO?
Várias empresas ainda contam com máquinas manuais, automáticas, semi automáticas e inclusive muito automatizadas. Atualmente existem máquinas de um passo que são chamadas 2-1-2 que são duas de enchimento de concentrado, uma crimpadora ou seladora, ou dosadora de propulsor.
O passo duplo passa a ser 4-2-4 com quatro dosadoras de concentrado, duas crimpadoras ou seladoras e quatro dosadoras de propulsor.
2. CICLO DE VIDA
O ciclo de vida ou projeto nasce de uma necessidade através de uma demanda de produção ou demanda de um cliente.
A partir daí começa com a viabilidade que é analisar a necessidade para o projeto que estamos apresentando como tal. Continua com o desenho dos equipamentos que serão instalados nesta máquina de aerossol para o passo duplo, em seguida passamos a execução, que já é a instalação dos equipamentos escolhidos. Depois segue a operação que é onde o equipamento é iniciado como tal é um passo duplo e é a execução como tal de reinstalação para poder iniciar.
O passo seguinte é a operação de tais equipamentos colocados nessa máquina de aerossol, em seguida vem a avaliação onde se mede o esperado de tal necessidade que temos como princípio do projeto como tal. E para finalizar vêm as conclusões que é onde vemos se a necessidade inicial é a esperada , se foi real foi o que buscávamos.
3. SISTEMAS DE PRODUÇÃO:
CONTÍNUA:
Automatização.
Corridas longas.
Baixos inventários.
POR LOTES:
Flexibilidade.
Mudanças rápidas.
Altos níveis de inventário.
Por isso é importante a automatização das máquinas para subir a produção, um pouco acima, para subir 50 peças por minuto.
4. IDENTIFICAÇÃO DA NECESSIDADE
É começar a ver de onde nasceu e o que é que vamos ocupar para essa necessidade como tal ou projeto. É o incremento da Produção e da Rentabilidade , é por ele que é requerido ter um passo duplo e buscar a rentabilidade do produto ou da empresa.
5. OBJETIVO
Incrementar a produção com a mesma equipe operacional de linha e sem ter que modificar o espaço físico com o qual se conta atualmente para o equipamento.
6. SITUAÇÃO ATUAL DO EQUIPAMENTO
Conta com 2 dosadoras a granel, uma crimpadora (engargoladora) e 2 dosadores de propulsor.
7. ALTERNATIVA
A opção proposta para a atualização desse equipamento, é incrementar 4 dosadoras a granel, duas seladoras e 4 dosadores de propulsor.
8. DESENHO
Medição da pressão do sistema pneumático e propulsor, as linhas antes e depois da implementação.
Tem que existir uma certeza de que com este equipamentos pode se iniciar o projeto. É muito importante ter manômetros certificados interna e externamente e que sejam reais para o equipamento nos quais serão colocados.
Existem manômetros de glicerina para evitar as batidas, manômetros secos para que seja real a medição do ar. Nesse caso existem dois tipos mais de manômetros que podem ser utilizados, tem que ver e analisar o compressor com o qual se conta atualmente no equipamento, se é o adequado ou não, por isso tem que ser avaliado profundamente.
No caso de uma crimpadora, no processo de um aerossol, seu ponto mais importante é que esteja bem encrimpado. Se não está bem selado, haverá rejeição, vazamentos e muitos problemas.
Deve-se levar em conta que os ajustes do equipamento devem ser 100% compatíveis com o padrão de selado ou com as especificações internas disponíveis para um selado bem crimpado.
Também é de extrema importância que seja avaliado o equipamento de fornecimento de propulsor, porque atualmente estão sendo dados 30 golpes por minuto e existe a pretensão de subir para 50. Se as bombas que se tem não dá para 50, tem que analisá-las para poder modificá-las.
Temos que ver os pistões de dosagem de propulsor que cumpram a checagem com a sua devida manutenção preventiva. É sugerido que seja semestral para que tenha mais qualidade de enchimento, o que são as máquinas de enchimento de concentrado. Nesse caso das máquinas seladoras deve ser de três meses para garantir um crimpado hermétrico, para que se tenha mais confiança do nosso processo e quanto as gaseificadoras têm checagem anti retorno que são onde se mede quanto propulsor vai ser injetado. Se se tem uma checagem que esta retornando em média, um ou dois gramas, isso é uma variação do propulsor. Por isso é indispensável ter no programa, todas as checagens anti retorno.
9. EXECUÇÃO
É importante que os pistões de dosagem tenham sua manutenção adequada para que faça o selado hermético, inclusive quando se injeta ao pote o concentrado, nesse momento existe uma checagem anti retorno que deve ter os programas suficientes de manutenção.
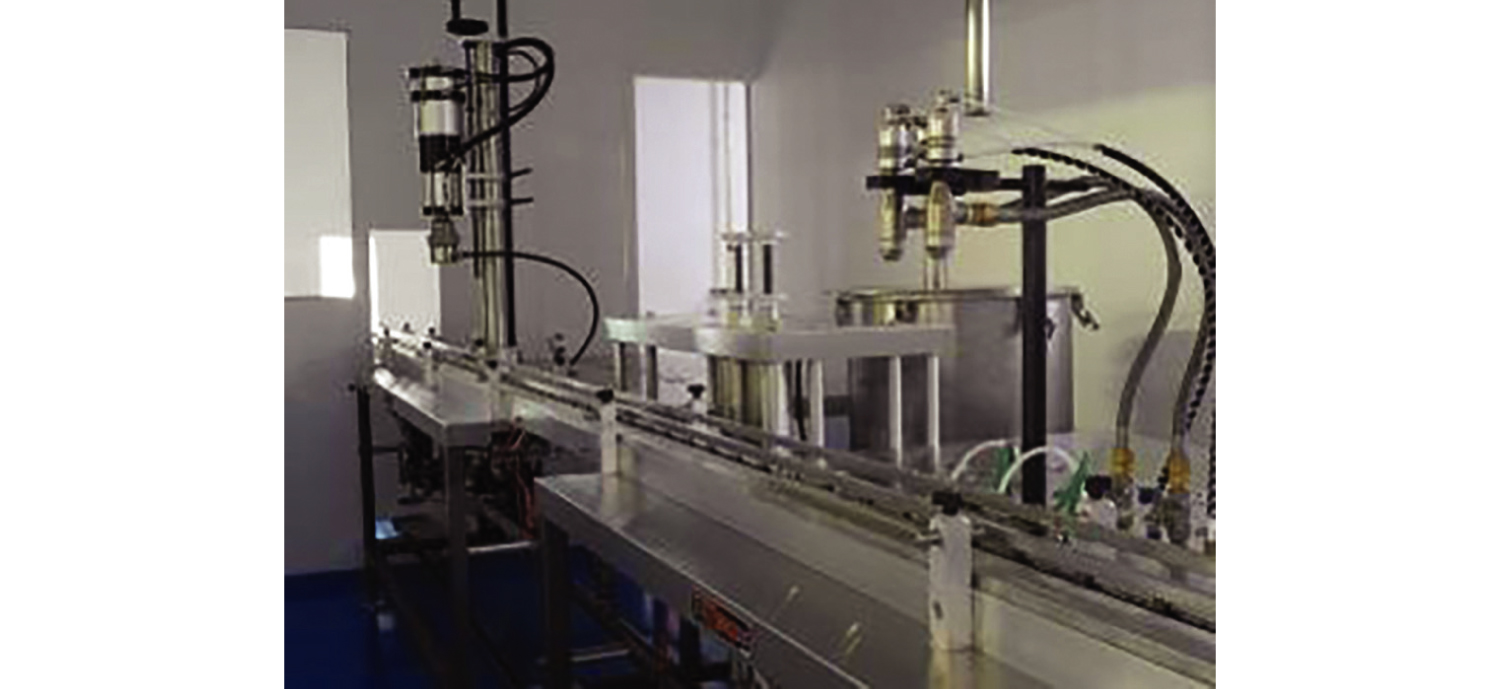
As dosadoras de propulsor são as que nos dará a pressão da embalagem para que saia o produto e seja expulso na sua totalidade.
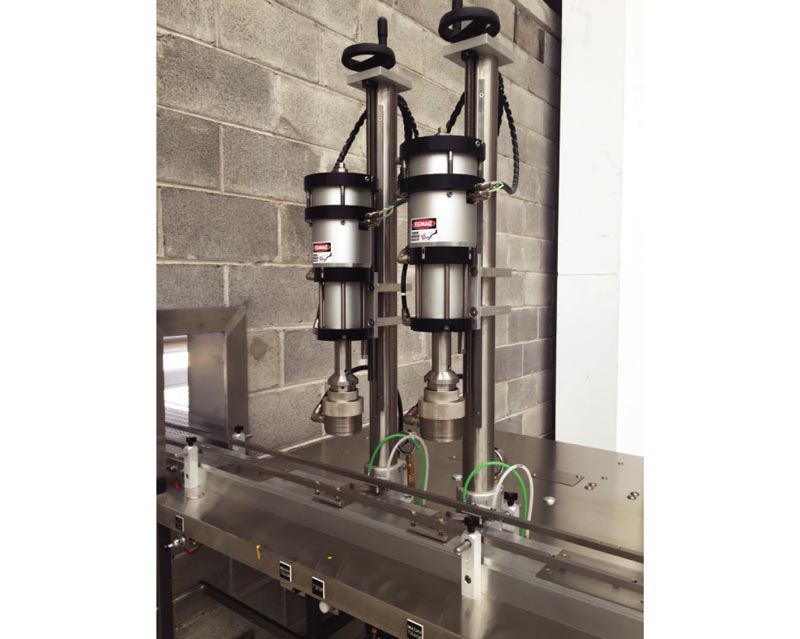
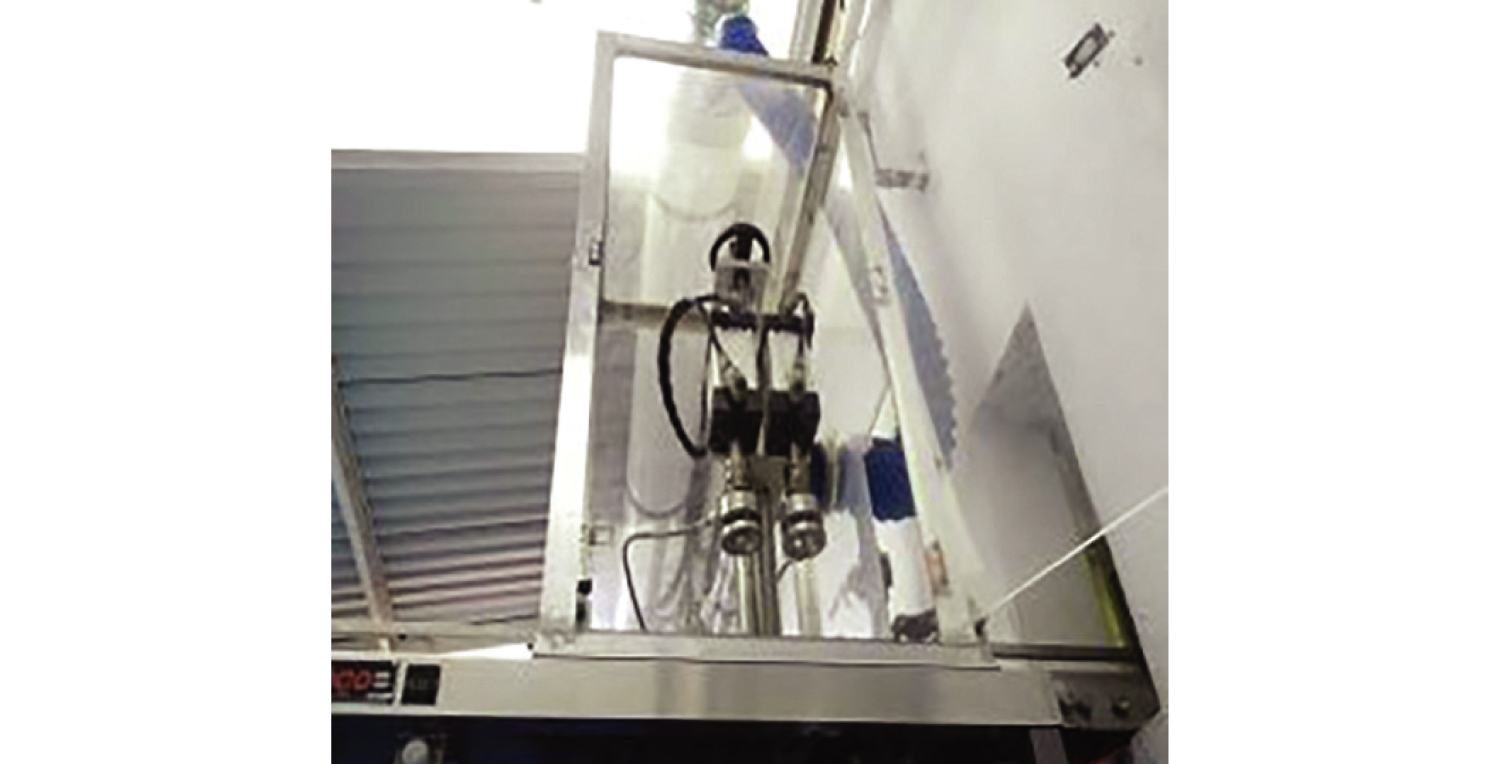
10. IMPLEMENTAÇÃO DA MELHORA
Esse é o 4-2-4. São observadas quatro dosadoras de concentrados.
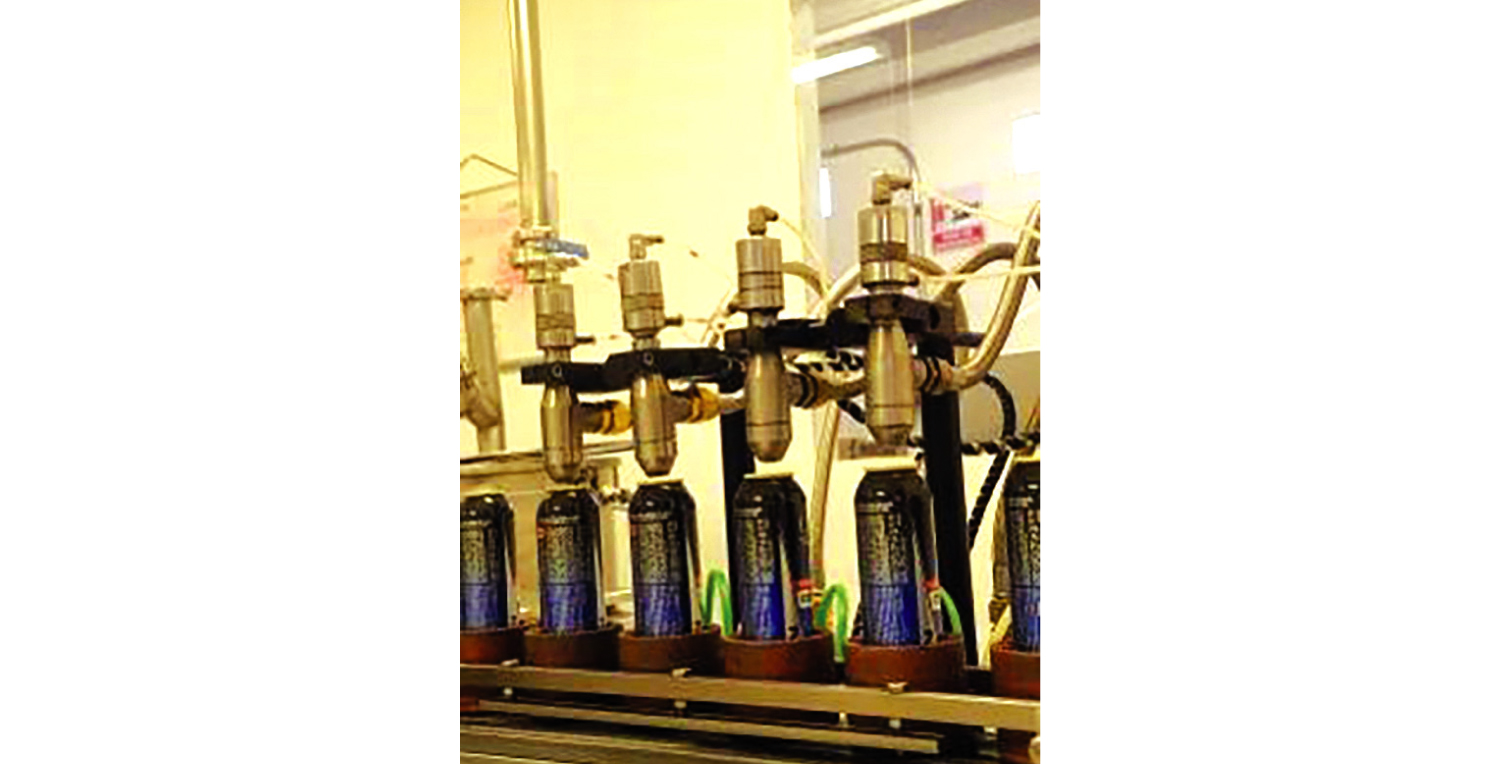
Essas são duas seladoras que já foram colocadas em sua totalidade. Os ajustes são os que irão garantir o processo.
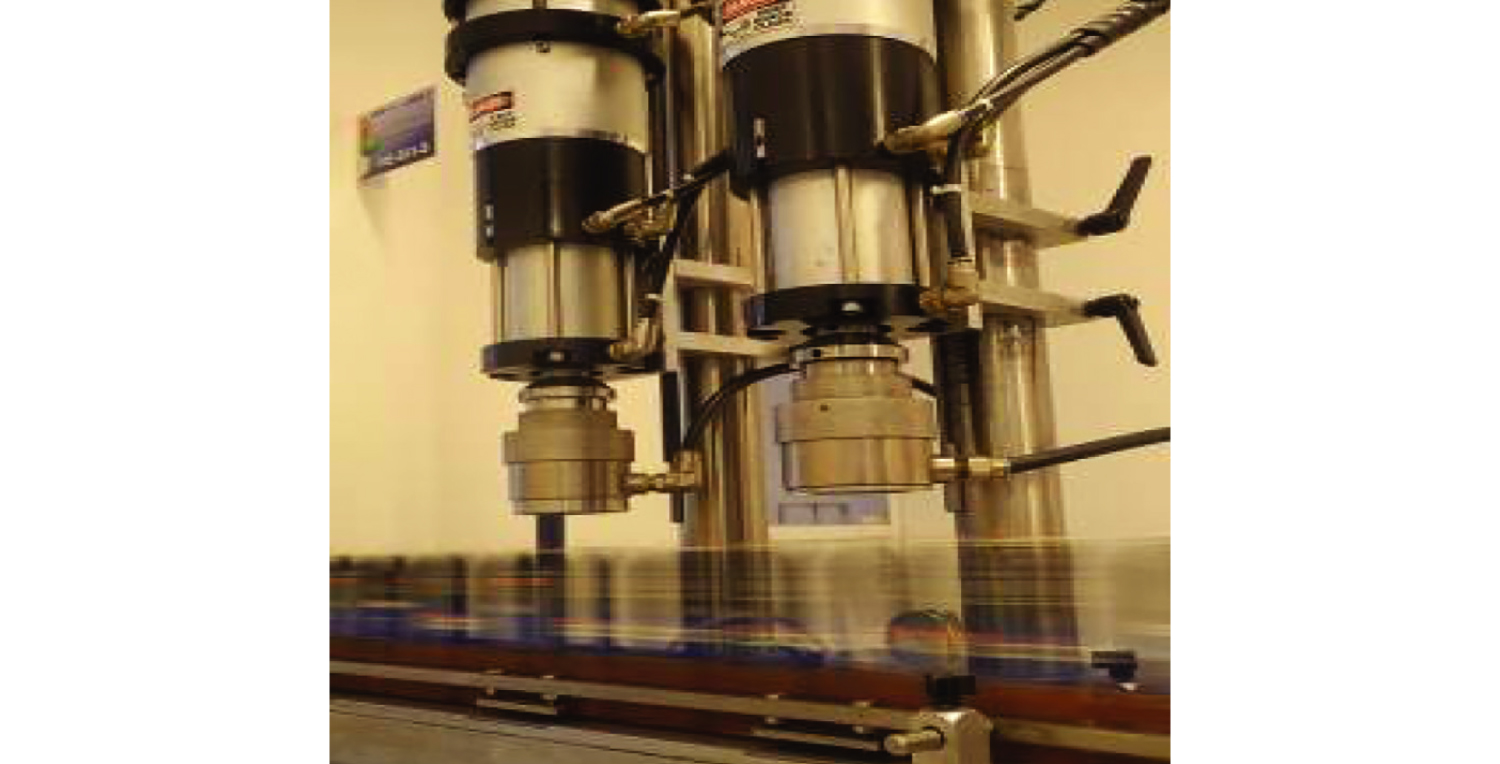
11. AVALIAÇÃO
São avaliados quatro pontos importantes:
Custo por Unidade Produzida
• Mão de obra direta.
• Custo de energia.
• Depreciação de equipamentos e infraestrutura.
• Custos indiretos.
12. RESULTADOS OBTIDOS
Baseado em 20 dias laborais ao mês e um turno de operação:
• Velocidade anterior: 30 ppm
• Velocidade atual: 50 ppm
• Crescimento: 66%
• Economia por cada unidade produzida:
31% do custo.
13. TEMPO DE RETORNO DA INVERSÃO
22.09 meses=1.84 años
14. CONCLUSÕES
O resultado obtido foi maior do que o esperado, porque o formato do recipiente, é o mesmo para todos os produtos e com dois formatos de tampa.Portanto, a implementação da mudança proposta é considerada viável, rentável e recomendável.