Aumento de la productividad con un doble paso máquina aerosol
Cada vez es mayor la demanda de producción de los aerosoles, por ello, las empresas fabricantes tienen que optimizar sus métodos para obtener excelentes resultados. Existen varios procedimientos para aumentar estas demandas. Uno de ellos es el Aumento de la Productividad con un doble paso en Máquina de Aerosol, tema que se impartió en el pasado Seminario Técnico del Aerosol y que hoy publicamos íntegramente.
ÍNDICE
1. ¿Qué es un doble paso?
2. Ciclo de Vida
3. Sistema de producción
4. Identificación de la necesidad
5. Objetivo
6. Situación actual del equipo
7. Alternativa
8. Diseño
9. Ejecución
10. Implementación de la mejora
11. Evaluación
12. Resultados Obtenidos
13. Tiempo de retorno de la inversión
14. Conclusiones
1. ¿QUÉ ES UN DOBLE PASO?
En varias empresas aún cuentan con máquinas manuales, automáticas, semiautomáticas e incluso muy automatizadas. Actualmente hay máquinas de un paso que se les llama 2-1-2 que son dos llenadoras de concentrado, una crimpadora o selladora, o dosificadoras de propelente.
El doble paso pasa a ser 4-2-4 con cuatro dosificadoras de concentrado, dos crimpadora o selladoras y cuatro dosificadoras de propelente.
2. CICLO DE VIDA
El ciclo de vida o proyecto nace de una necesidad a través de una demanda de producción o demanda de un cliente.
De ahí empieza con la factibilidad que es analizar la necesidad para el proyecto que estamos presentando como tal. Se continúa con el diseño de los equipos que se van a instalar en esta máquina de aerosol para el doble paso, en seguida pasamos a la ejecución, que ya es la instalación de los equipos que se eligieron. Después sigue la operación que es donde se pone en marcha el equipo como tal es un doble paso y es ejecución como tal de reinstalación para ponerse en marcha.
El siguiente paso es la operación de tales equipos puestos en esta máquina de aerosoles, luego viene la evaluación donde se mide lo esperado de tal necesidad que tenemos como principio del proyecto como tal. Y para finalizar vienen las conclusiones que es dónde se ve si lo de la necesidad inicial es lo esperado, si fue lo real fue lo que buscábamos.
3. SISTEMAS DE PRODUCCIÓN:
CONTINUA:
Automatización.
Corridas largas.
Bajos inventarios.
POR LOTES:
Flexibilidad.
Cambios rápidos.
Altos niveles de inventario.
Por eso es importante la automatización de las máquinas para subir la producción, un poco arriba, para subir 50 piezas por minuto.
4. IDENTIFICACIÓN DE LA NECESIDAD
Es empezar a ver de dónde nació y qué es lo que vamos a ocupar para esta necesidad como tal o proyecto. Es el Incremento de la Producción y de la Rentabilidad, es por ello que se requiere tener un doble paso y buscar la rentabilidad del producto o de la empresa.
5. OBJETIVO
Incrementar la producción con el mismo personal operativo de la línea y sin tener que modificar el espacio físico con el que se cuenta actualmente para el equipo.
6. SITUACIÓN ACTUAL DEL EQUIPO
Se cuenta con 2 dosificadoras de granel, una crimpadora (engargoladora) y 2 dosificadores de propelente.
7. ALTERNATIVA
La opción propuesta para la actualización de este equipo, es incrementar a 4 dosificadoras de granel, dos selladoras y 4 dosificadores de propelente.
8. DISEÑO
pelente, las líneas antes y después de la implementación.
Se tiene que tener la certeza que con este equipo se puede iniciar el proyecto. Es muy importante tener manómetros certificados interna y externamente y que sean reales para el equipo en los que serán colocados.
Hay manómetros de glicerina para evitar el golpeteo, manómetros secos para que sea la medición real del aire. En este caso hay dos tipos más de manómetros que pueden ser utilizados, hay que ver y analizar el compresor del que se cuenta actualmente para el equipo, si es el adecuado o no, por eso se tiene que evaluar profundamente.
En el caso de una crimpadora, en el proceso de un aerosol, su punto más importante es que esté bien encrimpado. Si no está bien sellado, se tendrán rechazos, fugas y muchos problemas.
Se debe que tener en cuenta que los ajustes del equipo deben de ser al 100% de cumplir con la norma del sellado o con las especificaciones internas que se tienen para un sellado bien crimpado.
También es de suma importancia que evaluemos el equipo de suministro de propelente, porque actualmente se están dando 30 golpes por minuto y se pretende subir a 50. Si las bombas que se tienen no dan para 50, hay que analizarlas para poder modificarlas.
Tenemos que ver los pistones de dosificado de propelente que cumplan los checks con su debido mantenimiento preventivo. Se sugiere que sea semestral para que tenga más calidad de llenado, lo que son las llenadoras de concentrado. En el caso de las selladoras debe de ser de tres meses para garantizar en crimpado hermético, para que se tenga más confianza de nuestro proceso y en cuanto a las gasificadoras se tienen checks anti-retorno que son dónde se mide cuánto propelente se va a inyectar. Si se tiene un ckeck que este retornando medio, uno o dos gramos, eso es una variación del propelente. Por eso es muy indispensable tener en el programa, todos los checks anti-retorno.
9. EJECUCIÓN
Es importante que los pistones de dosificación tengan su mantenimiento adecuado para que haga el sellado hermético, incluso cuando se inyecta al bote el concentrado, en ese momento hay un check antiretorno que debe tener los suficientes programas de mantenimiento.
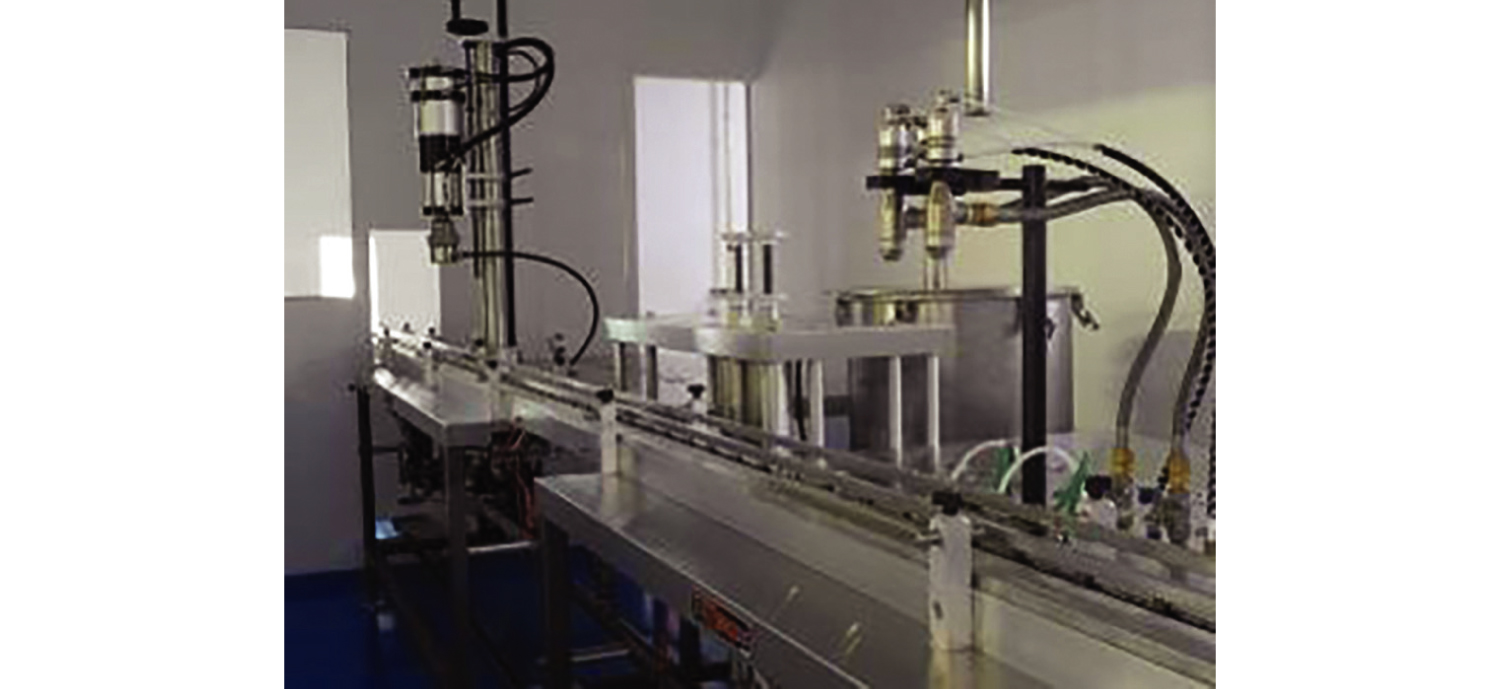
Las dosificadoras de propelente es la que nos dará la presión del envase para que salga el producto y sea expulsado en su totalidad.
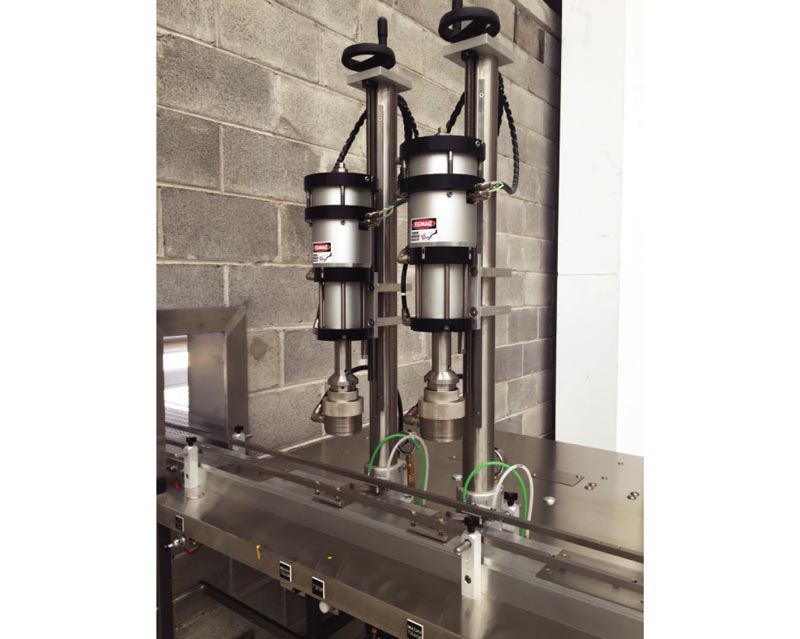
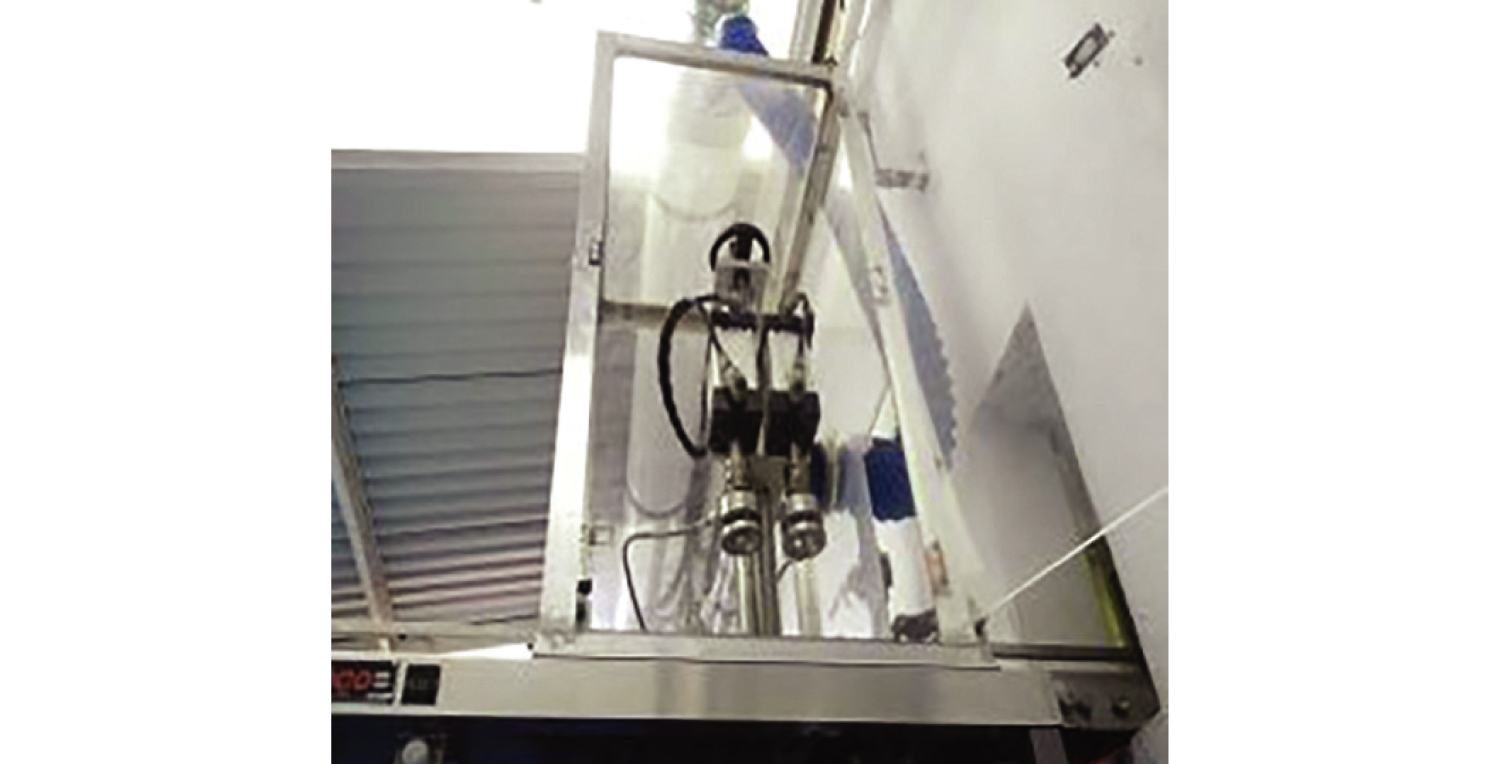
10. IMPLEMENTACIÓN DE LA MEJORA
Este es el 4-2-4. Se observan cuatro dosificadoras de concentrado
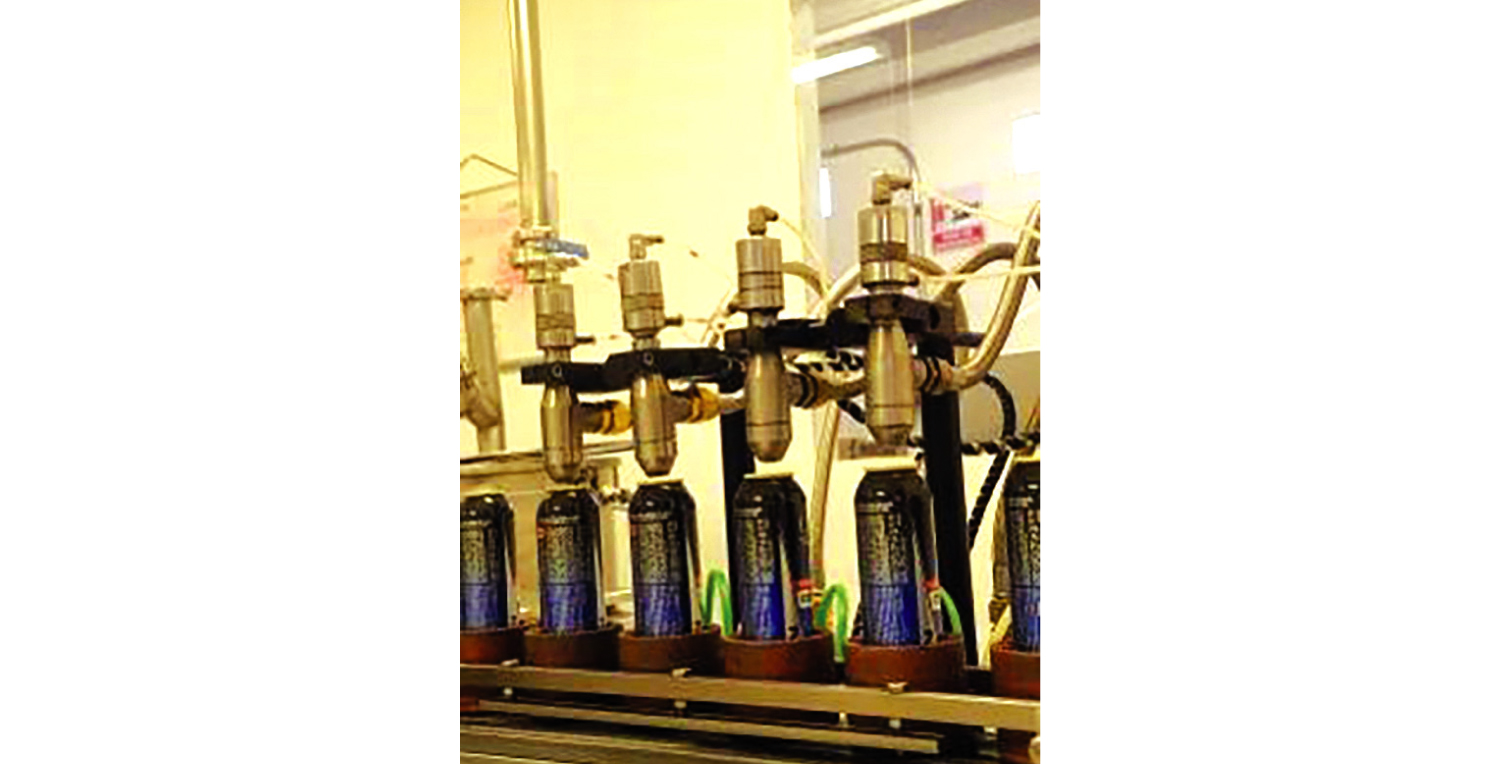
Estas son las dos selladoras que ya fueron colocadas en su totalidad. Los ajustes son los que van a garantizar el proceso.
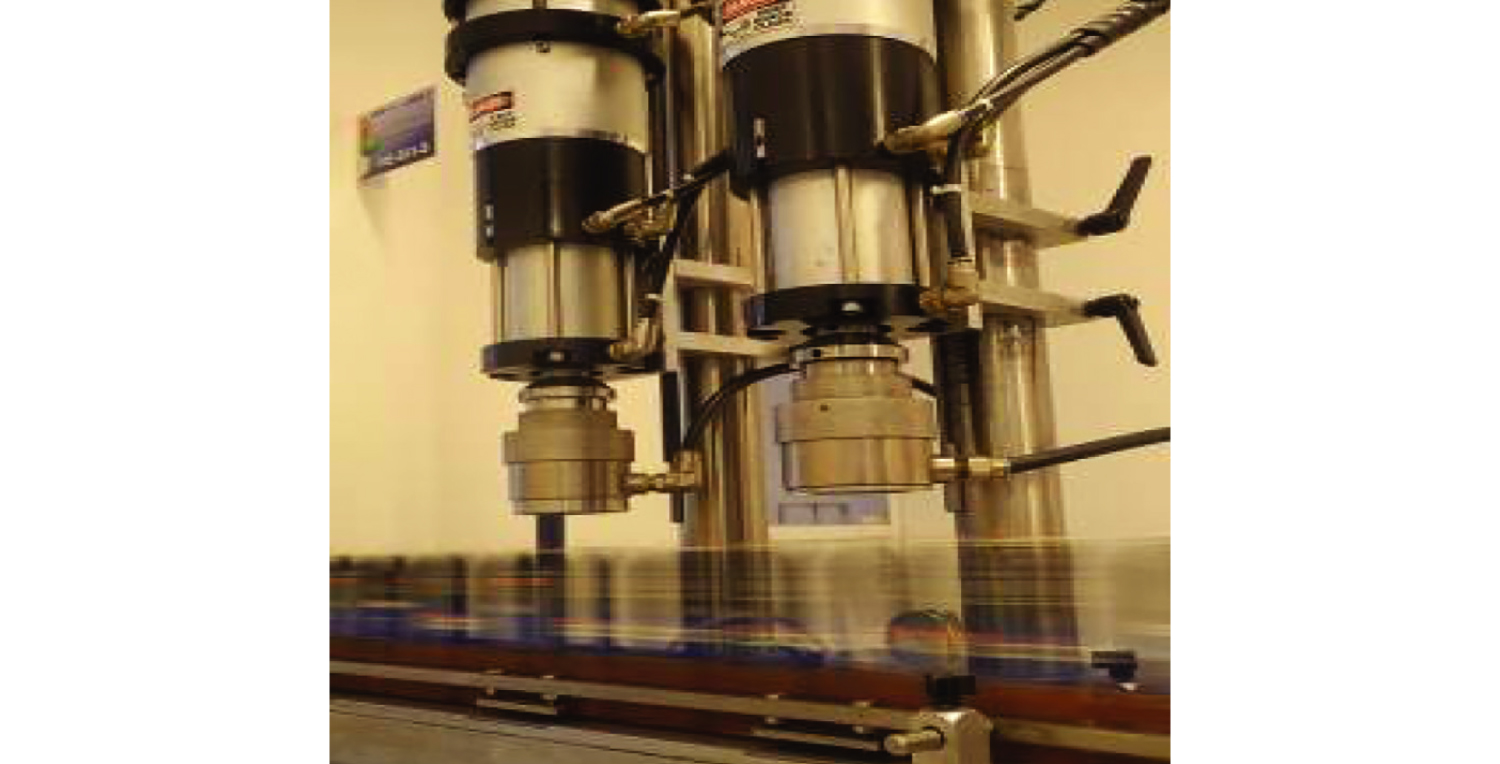
11. EVALUACIÓN
Se evalúan cuatro puntos importantes:
Costo por Unidad Producida
• Mano de obra directa
• Costo de energía.
• Depreciación de equipos e infraestructura.
• Costos indirectos
12. RESULTADOS OBTENIDOS
En base a 20 jornadas laborales al mes y un turno de operación:
• Velocidad anterior: 30 ppm
• Velocidad actual: 50 ppm
• Incremento: 66%
• Ahorro por cada unidad producida:
31% del costo.
13. TIEMPO DE RETORNO DE LA INVERSIÓN
22.09 meses=1.84 años
14. CONCLUSIONES
El resultado obtenido fue mayor a lo esperado, porque el formato del envase, es el mismo para todos los productos y con dos formatos de tapa. Por lo tanto, la implementación del cambio propuesto se considera factible, rentable y recomendable.