Seguridad en el cuarto de gasificación (Parte 1)
En los años 40s, cuando aparecieron los aerosoles, se utilizaron los clorofuorocarburos (CFCs) como propelentes, debido principalmente a que no eran inflamables y totalmente inocuos, por lo que era posible llenar aerosoles prácticamente en cualquier lado.
Posteriormente, en los años 50s se comenzaron a utilizar los hidrocarburos como propelentes (n-butano, isobutano y propano y mezclas de los mismos). Esto fue por razones de costos y para facilitar el envasadode productos con base acuosa. Hay que tomaren cuenta que estos hidrocarburos también tienen las ventajas de ser totalmente puros e inodoros. (A partir de aquí nos referiremos a estos propelentes como HAPs –Hydrocarbon Aerosol Propellants–).
Sin embargo, con todo y estas propiedades encontradas en los HAPs, también se les hallaron dificultades, debido a su alto nivel de inflamabilidad y explosividad. De tal manera que en aquellos años existían tres tipos de envasado de aerosoles:
- Los que envasaban dentro de la planta.
- Los que envasaban fuera de la planta –en bunker / cuarto seguro, especial–.
- Los que envasaban fuera de la planta, al aire libre.
Aquí es donde traemos a cuenta al conocido “TRIÁNGULO DE FUEGO”:
Como el oxígeno siempre está presente en el aire, hay que tomar medidas extremas. Así que el envasado de HAPs requiere que siempre se use doble control de seguridad:
- La ventilación es primordial para evitar una concentración riesgosa de HAPs (el combustible). Hay que tomar en cuenta que los HAPs son inflamables en aire, dentro de los límites aproximados de 1.8% (límite inferior de explosividad o “lower explosive limit – LEL”) y 9.5% (límite superior de explosividad o “upper explosive limit – UEL”). Por ello tratamos de evitar en las plantas de envasado de aerosoles que la concentración nunca se acerque al límite inferior (LEL).
- Un control sistemático para evitar todas las fuentes de ignición.
En una planta típica de aerosol, se hacen todos los esfuerzos para evitar la fuga de HAPs, sin embargo, las tuberías y mangueras terminan por romperse, incluso si están perfectamente mantenidas. Siempre habrá algunas “fugas” de envases que tienen válvulas defectuosas, o de envase defectuoso, o existe un daño en la válvula causado por el adaptador de gasificación.
Debido a esto, el hidrocarburo siempre puede estar presente, por ello es muy importante que no exista una fuente de ignición mientras se disipa el gas. Esta declaración general se aplica al llenar HAPs en cualquier lugar –y también se aplica a otros propelentes inflamables, como dimetil éter.
Presentamos las tres alternativas, sus ventajas y desventajas:
Llenado de hidrocarburos dentro de la planta
Hay que mencionar que aunque conozcamos tres opciones, en realidad solo hay dos, porque el envasado de hidrocarburos dentro de la planta ha sido totalmente desacreditado y sabemos que ninguna de las plantas de aerosoles importantes, construidas en los últimos veinte años, cuenta con gasificación en interior.

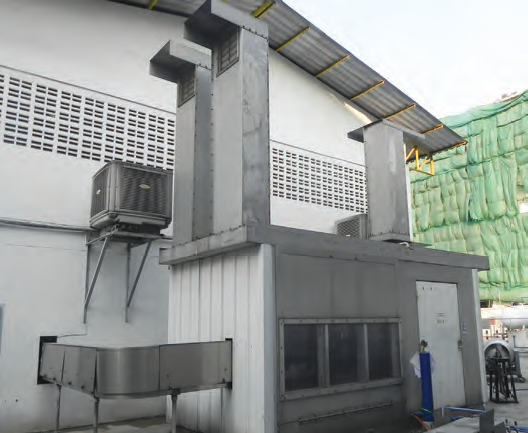
Las pocas plantas que aún tienen instalaciones para envasado de HAPs en el interior cuentan con la misma ventilación y los mismos estrictos controles de seguridad que las que envasan en el exterior.
Cuartos seguros de gasificación externos
La tercera opción, que aparecerá en el próximo número de AEROSOL la revista. En este punto, existen casos en que el clima, normas gubernamentales, o normas de la propia empresa no permiten la gasificación al aire libre por lo que utilizar el sistema de llenado en cuartos seguros de gasificación externos es una buena opción.
El diseño para el cuarto de gasificación
El cuarto de gasificación es el área de la planta donde se manipula “el material” más inflamable, por lo que su diseño debe de permitir el suficiente espacio para la maquinaria de operación y el personal que opera en el lugar, así como para llevar a cabo el mantenimiento. Debe ser diseñado para prevenir y/o controlar derrames de emergencia, errores de los empleados y fallas en los equipos. Una novedad importante de la última década es que los proveedores de maquinaria de llenado de aerosoles están ofreciendo cuartos modulares de gasificación seguros, que cuentan con características que cumplen con los siguientes requisitos:
Ubicación del cuarto de gasificación
El cuarto de gasificación debe de estar separado del edificio principal y situado lo más lejos posible de fuentes de ignición. Además de aislar la sala de gasificación, siempre debe de estar ubicado en planta baja, sin una bodega o espacio debajo y sin drenajes de piso.
Construcción del cuarto de gasificación
Un cuarto exterior de gasificación puede ser construido de dos maneras. En primer lugar, las cuatro paredes y el techo se construyen para soportar 490 kg. por metro cuadrado, con un panel de alivio. El otro diseño consiste en que cualquier pared frente al edificio principal debe tener los 490 kg. por metro cuadrado, mientras que las otras tres paredes pueden ser de material de resistencia menor, siempre y cuando exista un panel de alivio que pueda abrirse a 49 kg. por metro cuadrado, o menos, en una zona aislada. El tamaño de los paneles de alivio son equivalentes a un metro cuadrado por cada 15 metros cúbicos de volumen del cuarto. Es importante que el panel de alivio no sea bloqueado con mercancía. En caso de explosión, este panel puede salvar vidas.
Ventilación en el cuarto de gasificación
La clave para una operación segura durante el llenado con HAPs, es una ventilación adecuada dentro el cuarto de gasificación y también en las áreas inmediatamente cercanas. La ventilación se especifica considerando el tamaño del área y estimando la fuga que pueda ocurrir del equipo de llenado y las latas dañadas, con cierto margen de error. La mayoría de los cuartos de gasificación son pequeños y un cambio completo de aire por minuto es suficiente.
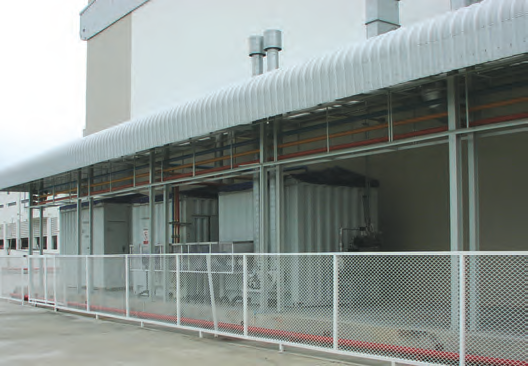
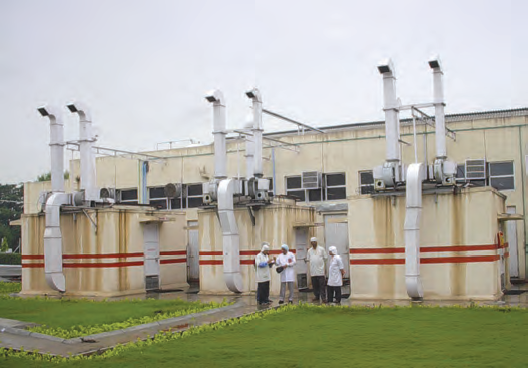
Sin embargo, los ductos deben ser diseñados para el flujo de tres cambios de aire por minuto, debido a que durante las emergencias es necesaria una extracción adicional para reducir la acumulación de HAPs. El diseño de ventilación debe permitir que todas las puertas estén cerradas durante las operaciones. Debe estar funcionando un sistema que active una alarma o parar la máquina, si alguna puerta permanece abierta. Debido a que el propelente es inodoro e invisible, el ventilador de servicio tiene que estar funcionando durante todas las operaciones de envasado. No es aceptable que la ventilación funcione sólo en caso de emergencia.
El aire de la ventilación debe ser aspirado a nivel del suelo y debe haber una entrada de aire fresco del lado opuesto. La máquina de gasificación debe colocarse directamente en la trayectoria del flujo de aire para evitar bolsas de vapor de aire y gas estacionado. El aire de escape debe ser liberado al exterior al menos dos metros por encima del nivel del techo. No estarán permitidas todas las entradas de aire o aberturas debajo o dentro de los cinco metros del ducto de escape.
Si el cuarto de gasificación está pegado a la planta, la misma planta debería tener presión positiva siempre, de tal manera que el aire fluya de la planta al cuarto de gasificación y no al contrario. La ventilación de la planta no debe sacar el aire del cuarto de llenado, ya que este podría contener gas. Un indicador de tela o de papel que puede ser colocado frente a las aberturas de las bandas transportadoras de envases, hará saber la dirección del flujo de aire, dentro o fuera del cuarto de gasificación.
El aumento del flujo de aire en una emergencia se lleva a cabo mediante la activación de una segunda velocidad del ventilador, o bien, mediante la activación de un segundo ventilador. Esta activación de ventilación adicional se puede lograr con un interruptor manual situado cerca de la máquina de carga o de forma automática activada por el sistema de detección de fugas. El ventiladorde emer
gencia y otras alarmas deben de estar vinculadas a los dispositivos de detección de gas que detectan el propelente cuando se acumula en el cuarto de gasificación. Este dispositivo debe ser lo suficientemente flexible para activar las alertas y sirenas cuando se alcanzan determinados niveles que marcan el límite porcentual inferior de explosividad (LEL).
También son convenientes pulsadores manuales para evitar riesgos adicionales cuando se produce un incendio o existe una emergencia en alguna de las áreas de la planta. Estos pulsadores deben ser ubicados en sitios de fácil acceso, cuando exista la necesidad de una evacuación. Las manijas de las puertas deben ser de un tipo de liberación rápida, de manera que en caso de emergencia no entorpezcan la evacuación rápida del personal que se encontraba dentro del cuarto de gasificación. Las puertas deben abrir hacia el exterior del cuarto, por la misma razón.
Equipos de detección de gas
La instalación correcta de los sensores de gas permitirá conocer la acumulación de gas en un cuarto de gasificación cerrado y reaccionar. No deben ser ubicados cerca de las áreas obvias de posibles fugas. Se deben ubicar estos sensores por encima de la corriente principal del aire, aproximadamente de 15 a 25 cms., lejos de las cabezas de carga, bombas de llenado, las aberturas de ventilación y los ductos de escape. Una ubicación excelente para un sensor de gas es debajo de las aberturas de la banda transportadora. Otra, arriba de los conductos de aire, al lado de la banda transportadora.
Es esencial que los detectores de gas se prueben cuando menos una vez a la semana para saberque funcionan correctamente y se compruebe que registran los porcentajes mínimos LEL. De igual manera se deben de probar con frecuencia todos los dispositivos de emergencia.
En el diseño de los procedimientos de emergencia, el sistema de detección de gas que se utiliza, debe de funcionar conforme a los porcentajes de LEL, que controla diversas etapas de alarmas, ventilación e interruptores de propelente. Es muy raro encontrar este sistema en los países en desarrollo, aunque es extremadamente riesgoso operar sin la adecuada instalación de seguridad en un cuarto de gasificación cerrado.
En el siguiente listado se dan a conocer los típicos sistemas de detección de gas, por porcentajes de LEL:
- El ventilador secundario se pone en marcha para aumentar la ventilación de escape.
- Las señales de alarma de campana son una indicación de que existe una primera fase de emergencia.
Al 40% (LEL)
- Apagado automático de la válvula solenoide que cierra la entrada del propelente que viene desde el patio de tanques.
- La ventilación se incrementa (En caso de que se utilice un ventilador secundario de dos velocidades).
- Una alarma de sirena responde, indicando la evacuación de emergencia del cuarto de gasificación y el área inmediatamente cercana.
Si se cuenta con un sistema de seguridad diseñado para responder de la manera indicada, se evitará de forma segura una acumulación de gas por arriba de los niveles de HAPs, en el cuarto de gasificación.
Conexiones eléctricas y tierras
Por supuesto, en los casos de gasificación en interior como en exterior, es indispensable contar con un mínimo de conexiones eléctricas y que estas tengan el máximo grado de seguridad a prueba de explosión.
Los tanques de propelente, tuberías y bombas, así como la maquinaria para la gasificación deben de estar puestos a tierra. Un ingeniero especializado en este sistema deberá de encargarse de esta tarea.