Tendências no setor de embalagens na indústria de aerossol
Por Eduardo Weingärtner, Director de Datos – PackIOT
PhD del Instituto Federal Suizo de Tecnología de Zúrich (ETH).
Este artigo técnico contém a perspectiva da PackIOT e de outros players do mercado voltados para soluções e tendências para a indústria de embalagens, principalmente na produção de latas aerossóis, com foco na transformação digital desse segmento industrial.
A indústria de embalagens hoje ainda opera sob demanda e apresenta perdas de e ciência. Com esse cenário, as preocupações atuais com a sustentabilidade geram a necessidade de evitar desperdícios e alavancar a e ciência operacional, uma vez que os empreendimentos atuam diretamente nas métricas nanceiras das empresas.
ÍNDICE
1.- ¿Como identi car gargalos numa linha de produção de embalagens?
2- ¿Que fazer para superar um gargalo identificado?
1.- ¿COMO IDENTIFICAR GARGALOS NUMA LINHA DE PRODUÇÃO DE EMBALAGENS?
Imagine uma linha de produção onde apenas peças boas são produzidas (100% de qualidade), o mais rápido possível (100% de desempenho) e sem paradas (100% de disponibilidade). A e ciência global dos equipamentos (em inglês Overall Equipment Effectiveness, com a sigla OEE) seria igual a 100%, o que signi ca «produção perfeita». Embora sonhos possam se tornar realidade (100% OEE), uma produção perfeita é bastante rara e, em muitos casos, o sonho acaba se tornando um pesadelo para aqueles trabalhadores de “chão de fábrica” diretamente envolvidos na produção. Equipamentos/máquinas falham por diversos motivos, pessoas cometem erros e tudo isso junto torna praticamente impossível alcançar a perfeição.
A boa notícia é que sempre há espaço para melhorias, ou seja, sempre podemos melhorar a forma como fazemos as coisas. Com esse objetivo em mente, um processo de melhoria contínua deve ser implementado para tratar exatamente o que está impedindo uma linha de produção de ser perfeita. Em «Teoria das Restrições» (em inglês Theory of Constraints), Eliyahu M. Goldratt, autor do best- seller «A Metal» (em inglês The Goal), argumenta que é preciso seguir «As Cinco Etapas de Foco» para atingir seu objetivo (por exemplo, maximizar o desempenho geral):
• Identi car as restrições do sistema
• Decidir como explorar as restrições do sistema
• Subordinar tudo o mais às decisões anteriores
• Elevar/Eliminar as restrições do sistema
• Se uma restrição foi resolvida nas etapas anteriores, volte para a etapa um (ou seja, repita conforme necessário)
A teoria que acabamos de mencionar a rma que «o desempenho de qualquer sistema é determinado por uma restrição». Então, vamos começar do início e focar em como identi car essa restrição, ou seja, «o gargalo».
Considere uma linha de produção ilustrada na Fig. 1. Ela consiste em quatro máquinas e três acumuladores (acumuladores nitos, ou seja, podem armazenar apenas um número nito de peças). As peças discretas uem de M1 para M4 e visitam todas as máquinas e acumuladores em uma sequência xa, ou seja, cada máquina alimenta apenas um acumulador e cada acumulador alimenta apenas uma máquina. Não conformidades ou desperdício podem sair da linha após serem processados em cada máquina. A produção líquida durante um período de tempo especi cado é igual ao número de peças que entram na primeira máquina (produção bruta) menos a soma dos desperdícios produzidos na linha.
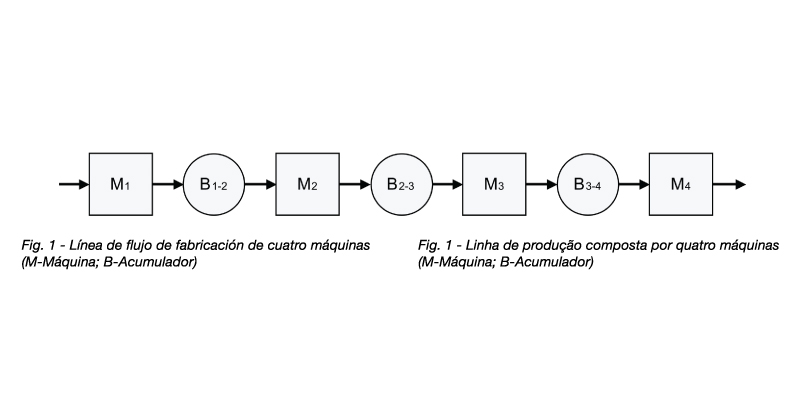
Este tipo de linha de produção representada na Fig. 1 é conhecido como «sistema assíncrono». As máquinas são, até certo ponto, desacopladas umas das outras devido aos acumuladores intermediários. Assim, cada máquina pode iniciar e parar de forma independente (assincronia), mesmo que tenham exatamente o mesmo tempo de ciclo, desde que os acumuladores vizinhos não estejam vazios nem cheios. Como as máquinas não estão totalmente desacopladas umas das outras, elas podem car bloqueadas (em inglês blocked) ou aguardando produtos do equipamento anterior (em inglês “starved”). Uma máquina está bloqueada se estiver operacional, mas o acumulador posterior está cheio, o que signi ca que nenhuma outra peça pode ser armazenada nela e a máquina é forçada a parar (em espera/standby).
Por outro lado, uma máquina está “starved”, se estiver operacional, mas o acumulador anterior estiver vazio, ou seja, não há peças disponíveis para serem processadas e a máquina para (em espera). Para ilustrar essa dinâmica, a Fig. 2 apresenta um exemplo simpli cado dos estados de uma máquina, suponha que seja a máquina M2 da Fig. 1, e o nível de armazenamento de seus acumuladores vizinhos, numa linha do tempo contendo seis «etapas de tempo»
numeradas de 0 a 6. No passo de tempo 0, M2 está ativa e os acumuladores não estão vazios nem cheios. Depois de um tempo, o nível de armazenamento de B1-2 começa a diminuir, provavelmente porque M1 parou devido a uma falha, até que o mesmo esteja completamente vazio na etapa de tempo 1.
Neste momento, M2 está “starved” e para de processar peças. Na etapa de tempo 2, M2 começa a processar as peças novamente. Logo depois, B2-3 começa a encher, provavelmente porque M3 ou M4 parou devido a uma falha, e enche-se completamente no passo de tempo 3 onde M2 se encontra bloqueada. A partir da etapa de tempo 4, M2 está ativo novamente até parar na etapa de tempo 5. Neste ponto, M2 não está “starved” nem bloqueado e, portanto, encontra-se em modo de falha. B1-2 enche e o B2-3 esvazia. Portanto, a Figura 2 ilustra uma dinâmica comum que deve ser seguida para avaliar o status de cada máquina em uma linha de produção.
Em termos de disponibilidade, os seguintes estados de máquina são possíveis (simpli cação), sendo que três deles são ilustrados na Fig. 2:
1. Ativo: a máquina está funcionando e processando peças; 2. Em Espera: a máquina está bloqueada ou aguardando peças (starved);
3. Falha: a máquina não está processando peças devido a uma falha;
4. Parada: a máquina está parada devido a uma atividade planejada, como setups, manutenção planejada, entre outras.
Esses quatro estados de nem o cenário e são cruciais para identi car o gargalo, porém um pouco outras informações ainda são necessárias. A razão para isso é que uma máquina ativa pode produzir refugo e/ou ter tempos de ciclo mais longos em comparação com outras máquinas. Portanto, os aspectos de disponibilidade, qualidade e desempenho devem ser levados em consideração na análise.
Uma solução possível é adaptar o cálculo do OEE. Ao invés de ter um OEE para toda a linha de produção, é preciso adaptar o cálculo para cada máquina. Vamos chamá-lo de OEEbd, que signi ca «OEE de detecção de gargalo». O OEEbd difere do OEE regular porque não considera o tempo de espera (idle) como parte do tempo disponível. Porque não? Porque quando uma máquina está em espera, ela ca nessa condição porque está restrita por outra máquina. Portanto, apenas o tempo ativo e o tempo de falha são considerados como tempo disponível e são usados para calcular OEEbd. No nal, a máquina com o OEEbd mais baixo em um determinado momento é considerada o gargalo naquele momento. É importante mencionar essa dependência do tempo, pois os gargalos também podem mudar de uma máquina para outra ao longo do tempo devido a diferentes motivos.
Vejamos um exemplo prático simpli cado, com base na linha de produção mostrada na gura 1. Suponha que seja uma linha de latas de aerossol, produzindo a uma taxa de produção máxima de 150 latas por minuto. Todas as máquinas possuem a mesma velocidade máxima, ou seja, o mesmo tempo de ciclo. Os dados de produção de trinta dias são resumidos na Tabela 1. As primeiras cinco linhas mostram o número cumulativo de dias que cada máquina esteve ativa, bloqueada, “starved”, parada ou em modo de falha.
A produção bruta dos trinta dias é de 4,2 milhões, que é o número de latas que entraram no M1 (ou foram prensadas na prensa de extrusão). A produção líquida e as taxas de desperdício/refugo correspondentes também são apresentadas na Tabela 1. O tempo disponível necessário para calcular OEEbd, conforme mencionado acima, é a soma do tempo ativo e do tempo de falha. A produção ideal é calculada com base no tempo disponível e seria
a “produção perfeita” para este tempo agregado especí co. Dado que a taxa de produção é de 150 latas por minuto (216.000 latas por dia), M1, por exemplo, teria uma produção ideal de 4.968.000 latas (23 dias multiplicados por 216.000). Como M1 produziu apenas 4.109.000 latas, sua pontuação OEEbd é de 82,7% (4.109.000 dividido por 4.968.000). Após repetir o mesmo cálculo para todas as máquinas, veri ca-se que o M2 possui o menor OEEbd (80,2%) e representa o gargalo para os trinta dias de produção. Outras informações interessantes podem ser vistas na Tabela 1:
Embora M1 e M2 tenham o mesmo tempo total de falha (3 dias cada), M2 tem a um OEEbd menor, já que M2 tem uma maior taxa de desperdício/refugo; Embora M3 tenha passado um dia a mais em modo de falha em comparação com o M4, ela tem o OEEbd mais alto. A razão para isso é que M4 tem uma taxa de desperdício três vezes maior do que a taxa de desperdício de M3.
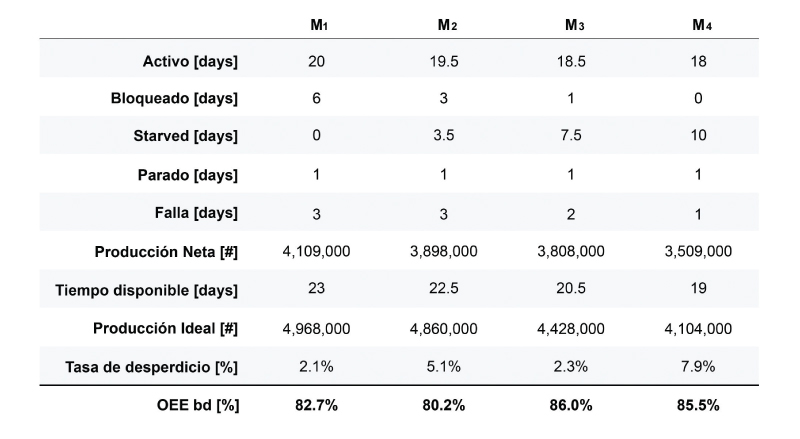
A tarefa de atribuir corretamente os diferentes estados a todas as máquinas é um grande desa o e não pode ser resolvido através de um simples processo de observação em linhas de produção rápidas, como é comum na indústria de embalagens. Uma grande quantidade de dados deve ser coletada, processada e analisada para que as informações corretas sejam obtidas.
2.- QUE FAZER PARA SUPERAR UM GARGALO IDENTIFICADO?
Agora que o gargalo foi detectado no exemplo anterior (Tabela 1), deve-se decidir como explorá- lo para aliviar a restrição. As primeiras sugestões vindas da tabela são «tempo de falha» e «taxa de desperdício».
No caso de tempo de falha, uma avaliação mais abrangente deve ser realizada para mapear as principais causas de falha / tempo de inatividade (diagnóstico de falha). Com base nisso, podem ser detectadas, por exemplo, falhas mecânicas e / ou elétricas intermitentes, de modo que um plano de ação adequado possa ser estabelecido para mitigar seus efeitos e aumentar o “tempo médio entre falhas” (em inglês “Mean Time Between Failures”). Minimizar o «tempo médio para reparo» (em inglês Mean Time to Repair) também é crítico.
Isso pode ser feito reduzindo o “Tempo de Resposta de Manutenção”, por exemplo, tendo alarmes automáticos que avisam a equipe de manutenção sobre falhas. A equipe de manutenção também deve seguir “procedimentos de manutenção padrão” para garantir tempos mínimos de reparo. Além disso, deve ser elaborado um “Plano de Manutenção Preventiva” com foco nas principais falhas detectadas. A capacitação e empoderamento de operadores/trabalhadores é outra estratégia importante para “rodar a sua fábrica” com mais e ciência. Fornecer aos operadores informações em tempo real sobre o que está acontecendo no chão de fábrica pode ajudá-los a tomar decisões mais rápidas e, consequentemente, aumentar a e ciência geral das linhas de produção.
As estratégias mencionadas acima são apenas algumas opções para iniciar a «batalha». Lembre- se: concentre-se em ganhos rápidos (quick wins) para obter benefícios imediatos. A principal causa da ine ciência de um equipamento não é necessariamente a mais fácil de se resolver. Tudo começa simples.
Em termos de desperdício/refúgio, uma abordagem muito semelhante à mencionada acima deve ser seguida. Mapeie primeiro. Pode
ser um problema com matérias-primas, ajustes/ con gurações inadequadas da máquina, parâmetros de processo incorretos ou até mesmo problemas com sistemas de controle de qualidade automatizados, para citar alguns. Portanto, os “quick wins” vêm em primeiro lugar e não se esqueçam de manter os operadores informados em tempo real. Eles estão sempre dispostos a ter o melhor desempenho nos turnos do dia / semana, e podemos ajudá-los fornecendo informações de qualidade.
Uma vez que o objetivo de qualquer empresa é obter maiores lucros, um bom começo em direção ao objetivo é identi car os gargalos. Existem oportunidades de melhoria em cada linha de produção. Reconhecer esse fato e buscar constantemente essas oportunidades é um passo importante na criação de uma cultura de melhoria contínua em sua organização.
Você sabe onde estão os seus gargalos?