Tendencias en el sector del embalaje en la industria del aerosol
Por Eduardo Weingärtner, Director de Datos – PackIOT
PhD del Instituto Federal Suizo de Tecnología de Zúrich (ETH).
Este artículo técnico contiene la perspectiva de PackIOT y otros players del mercado enfocada en soluciones y tendencias para la industria del embalaje, en especial, en la producción de latas de aerosol, enfocada en la transformación digital de este segmento industrial.
La industria del embalaje hoy en día todavía opera bajo demanda y tiene pérdidas de e ciencia. Con este escenario, las preocupaciones actuales por la sostenibilidad generan la necesidad de evitar el desperdicio y apalancar la e ciencia operativa, ya que los desarrollos actúan directamente sobre las métricas nancieras de las empresas.
ÍNDICE
1.- ¿Cómo identi car cuellos de botella en una línea de producción de latas de aerosol?
2- ¿Qué hacer para superar un cuello de botella identificado?
1.- ¿CÓMO IDENTIFICAR CUELLOS DE BOTELLA EN UNA LÍNEA DE PRODUCCIÓN DE LATAS DE AEROSOL?
Imagina una línea de producción en la que sólo se produzcan buenas piezas (100% de calidad), lo más rápido posible (100% de rendimiento) y sin paradas (100% de disponibilidad). La e cacia global del equipo (OEE) sería igual al 100%, lo que signi ca «producción perfecta». Aunque los sueños pueden hacerse realidad (100% OEE), la producción perfecta es muy rara y, en muchos casos, el taller de fabricación puede convertirse, en cambio, en una pesadilla para quienes participan directamente en la producción. Las máquinas fallan por varias razones, los humanos cometemos errores y todo esto en conjunto hace que sea imposible alcanzar la perfección.
La buena noticia es que siempre hay margen de mejora, es decir, siempre podemos mejorar la forma en la que hacemos las cosas. Con ese objetivo en mente, se debe implementar un proceso de mejora continua para abordar exactamente lo que impide que una línea de producción sea perfecta. En la «Teoría de las restricciones», Eliyahu M. Goldratt, autor del libro más vendido titulado «El objetivo», sostiene que uno debe seguir «Los cinco pasos del enfoque» para lograr su objetivo (por ejemplo, maximizar el rendimiento general):
• Identi car las restricciones del sistema
• Decidir cómo aprovechar las limitaciones del sistema
• Subordinar todo lo demás a las decisiones anteriores
• Aliviar las limitaciones del sistema
• Si en los pasos anteriores se ha roto una restricción, vuelve al paso uno (es decir, repite según sea necesario)
La teoría recién mencionada establece que «el rendimiento de cualquier sistema está determinado por una restricción». Por lo tanto, comencemos desde el principio y centrémonos en cómo identificar esta restricción o, en otras palabras, «el cuello de botella».
Considera una línea de producción como se ilustra en la Fig. 1. Consta de cuatro máquinas y tres acumuladores (acumuladores nitos, es decir, pueden almacenar sólo una cantidad nita de piezas). Las piezas discretas uyen de M1 a M4 y visitan todas las máquinas y acumuladores en una secuencia ja, o en otras palabras, cada máquina alimenta sólo un acumulador y cada acumulador alimenta una sola máquina. Las no conformidades o el desperdicio pueden salir de la línea después de ser procesados en cada máquina. La producción neta durante un período de tiempo especí co es igual a la cantidad de piezas que ingresan a la primera máquina (producción bruta) menos la suma del desperdicio producida en la línea.
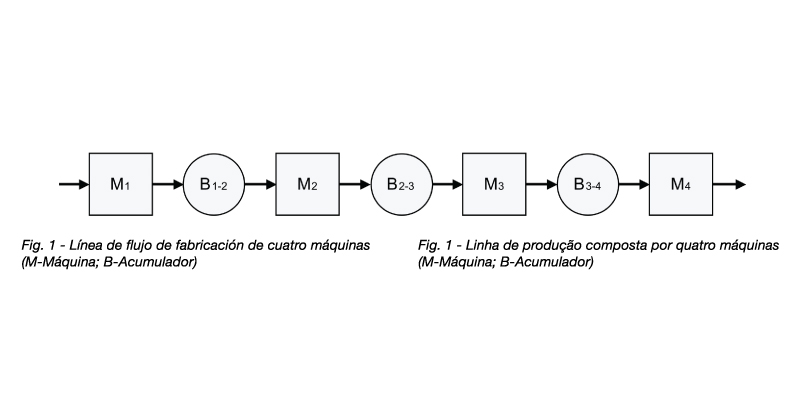
Este tipo de línea de producción representada en la Fig. 1 se conoce como «sistema asíncrono». Las máquinas están, hasta cierto punto, desacopladas entre sí debido a acumuladores intermedios. Así, cada máquina puede arrancar y parar de forma independiente (asincronía), incluso si tienen exactamente el mismo tiempo de ciclo, siempre que los acumuladores vecinos no estén vacíos ni llenos. Dado que las máquinas no están totalmente desacopladas entre sí, pueden bloquearse o starve. Una máquina está bloqueada si está operativa pero el acumulador posterior está lleno, lo que signi ca que no se pueden almacenar más piezas en ella y la máquina se ve obligada a detenerse (en espera).
Por otro lado, una máquina está starved, si está operativa pero el acumulador anterior está vacío, es decir, no hay piezas disponibles para ser procesadas y la máquina se detiene (en espera). Para ilustrar esta dinámica, la Fig. 2 presenta un ejemplo simpli cado del estado de una máquina, supongamos que es M2 de la Fig. 1, y el nivel de almacenamiento de sus acumuladores vecinos en una línea de tiempo que contiene seis «pasos de tiempo» numerados de 0a6.En el paso de tiempo 0, M2 está activo y los
acumuladores no están vacíos ni llenos. Después de un tiempo, el nivel de almacenamiento de B1-2 comienza a disminuir, probablemente porque M1 se detuvo debido a una falla, hasta que esté completamente vacío en el paso de tiempo 1.
En este momento M2 se encuentra starved y deja de procesar piezas. En el paso de tiempo 2, M2 comienza a procesar piezas nuevamente. Poco después, B2-3 comienza a llenarse, probablemente porque M3 o M4 se detuvieron debido a una falla, y se llena completamente en el paso de tiempo 3, donde M2 está bloqueado. Desde el paso de tiempo 4, M2 vuelve a estar activo hasta que se detiene en el paso de tiempo 5. En este momento, M2 no está starved ni bloqueado y, por lo tanto, está en modo de falla. B1-2 se llena y B2-3 se vacía. Por tanto, la gura 2 ilustra una dinámica común que debe seguirse para evaluar el estado de cada máquina en una línea de producción.
En términos de disponibilidad, son posibles los siguientes cuatro estados de la máquina (simpli cación) (tres de ellos se ilustran en la Fig.2):
1. Activo: la máquina está en funcionamiento y procesando piezas;
2. En espera: la máquina está bloqueada o starved; 3. Falla: la máquina está caída debido a una falla;
4. Detenido: la máquina está parada debido a una actividad plani cada, como montajes, mantenimiento plani cado, entre otros.
Estos cuatro estados establecen las bases y son cruciales para identi car el cuello de botella, pero todavía se requiere un poco más de información. La razón de esto es que una máquina activa puede producir desperdicio y/o tener ciclos más largos en comparación con otras máquinas. Por tanto, deben tenerse en cuenta los aspectos de disponibilidad, calidad y rendimiento.
Una posible solución es adaptar el cálculo de OEE. En lugar de tener un OEE para toda la línea de producción, uno tiene que adaptar el cálculo para cada máquina. Llamémoslo OEEbd, que signi ca «detección de cuellos de botella OEE». OEEbd se diferencia del OEE habitual porque no considera el tiempo de inactividad como parte del tiempo disponible. ¿Por qué no? Porque cuando una máquina se encuentra en estado de espera, está en esta condición porque está restringida por otra máquina. Por lo tanto, sólo el tiempo activo y el tiempo de falla se consideran como tiempo disponible y se utilizan para calcular OEEbd. Al nal, la máquina con la puntuación OEEbd más baja en un momento dado se considera el cuello de botella en ese momento. Es importante mencionar esta dependencia del tiempo, ya que los cuellos de botella también pueden cambiar de una máquina a otra debido a diferentes razones.
Veamos un ejemplo práctico simpli cado, basado en la línea de producción que se muestra en la gura 1. Supongamos que es una línea de latas de aerosol, que produce latas, a una tasa máxima de producción de 150 latas por minuto. Todas las máquinas tienen la misma velocidad máxima, es decir, el mismo tiempo de ciclo. Los datos de treinta días de producción se resumen en la Tabla 1. Las primeras cinco las muestran la cantidad acumulada de días en los que cada máquina estuvo activa, bloqueada, hambrienta, detenida o en modo de falla.
La producción bruta de los treinta días es de 4,2 millones de latas, que es la cantidad de latas que ingresaron a M1 (o fueron presionadas). La producción neta y las tasas de desperdicio correspondientes también se presentan en la Tabla 1. El tiempo disponible requerido para calcular OEEbd, como se mencionó anteriormente, es la suma del tiempo activo y el tiempo de falla. La producción ideal se calcula en base al tiempo disponible y sería
la “producción perfecta” para este tiempo agregado especí co. Dado que la tasa de producción es de 150 latas por minuto (216.000 latas por día), M1, por ejemplo, tendría una producción ideal de 4.968.000 latas (23 días multiplicado por 216.000). Dado que M1 produjo sólo 4,109,000 latas, su puntaje OEEbd es 82,7% (4,109,000 dividido por 4,968,000). Después de repetir lo mismo para todas las máquinas, se puede ver que M2 tiene la puntuación OEEbd más baja (80,2%) y representa el cuello de botella para los treinta días de producción. Se puede ver más información en la Tabla 1:
Aunque M1 y M2 tienen el mismo tiempo total de falla (3 días cada uno), M2 tiene la puntuación OEEbd más baja, ya que M2 tiene una tasa de desperdicio más alta; a pesar de que M3 pasó un día más en modo de falla en comparación con M4, tiene el OEEbd más alto. La razón de esto es que M4 tiene una tasa de desperdicio que es más de tres veces mayor que la tasa de desperdicio de M3.
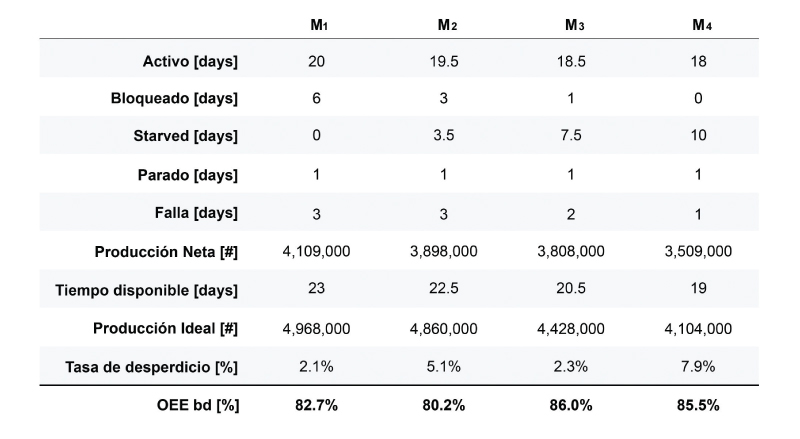
Tabla 1 – Cálculo de OEE bd para un tiempo de producción de treinta días
En realidad, la tarea de asignar correctamente los diferentes estados a todas las máquinas es un gran desafío. No se puede resolver mediante la simple observación en líneas de producción rápidas, como es habitual en la industria del embalaje. Se debe recopilar, procesar y analizar una gran cantidad de datos para que se pueda obtener la información correcta.
2.- ¿QUÉ HACER PARA SUPERAR UN CUELLO DE BOTELLA IDENTIFICADO?
Ahora que se ha detectado el cuello de botella en el ejemplo anterior (Tabla 1), se debe decidir cómo explotarlo para aliviar la restricción. Las primeras sugerencias de la tabla son «Tiempo de falla» y «Tasa de desperdicio».
En el caso del tiempo de falla, se debe realizar una evaluación más exhaustiva para mapear las principales causas de fallas/tiempo de inactividad (diagnóstico de fallas). En base a ello, se pueden detectar fallas mecánicas y/o eléctricas intermitentes, de modo que se pueda establecer un plan de acción adecuado para mitigar sus efectos y aumentar el “Tiempo medio entre fallas” general. También es fundamental minimizar el «tiempo medio de reparación».
Esto se puede hacer reduciendo el “Tiempo de respuesta de mantenimiento”, por ejemplo, al tener alarmas automáticas que noti quen al equipo de mantenimiento sobre fallas. El equipo de mantenimiento también debe seguir los “Procedimientos de mantenimiento estándar” para garantizar tiempos mínimos de reparación. Además de eso, se debe crear un “Plan de Mantenimiento Preventivo” enfocado en las principales fallas detectadas. El desarrollo de capacidades y el empoderamiento de los operadores/trabajadores es otra estrategia importante para administrar su fábrica de manera más e ciente. Brindar a los operadores información en tiempo real sobre lo que sucede en el taller puede ayudarlos a tomar decisiones rápidas y, en consecuencia, aumentar la e ciencia general de las líneas de producción.
Las estrategias mencionadas anteriormente son sólo algunas opciones para comenzar la «batalla». Recordatorio: enfócate en las ganancias rápidas para obtener bene cios inmediatos. La principal causa de la ine ciencia del equipo no es necesariamente la más fácil de abordar. Empieza simple.
En términos de desperdicio, debería seguirse un enfoque muy similar al mencionado anteriormente. Mapealo primero. Puede ser un problema con la materia prima, con un ajuste/con guración
inadecuados de la máquina, con parámetros de proceso incorrectos o incluso problemas con los sistemas de control de calidad automatizados, por mencionar algunos. Por lo tanto, las ganancias rápidas son lo primero y no olvides mantener informados a los operadores en tiempo real. Siempre están dispuestos a tener el mejor desempeño en turnos del día/semana, y puedes ayudarlos brindándoles información de buena calidad.
Como el objetivo de cualquier negocio es ganar más dinero, un buen comienzo hacia el objetivo es identi car los cuellos de botella. Existen oportunidades de mejora en cada línea de producción. Reconocer este hecho y esforzarse por encontrar constantemente estas oportunidades es un paso importante para crear una cultura de mejora continua en su organización.
¿Sabes dónde están tus cuellos de botella?