Segurança em fabricas do aerossois parte I
Dn Durante a vida útil do aerossol, desde o nascimento até o produto final, o conceito de segurança está particularmente envolvido durante a produção. Essa segurança é de grande importância no preenchimento, gaseificação e condicionamento; assim como em todas as tarefas realizadas no Aerossol, sem incluir a gaseificação, como o armazenamento de aerossóis, as diferentes etapas de transporte e tudo relacionado à coleta em centros de distribuição e pontos de venda. Também uso pelo consumidor e, finalmente, pós-tratamento do consumidor.
Por que falar da segurança em todas essas fases? O sistema aerossol tem uma particularidade quando comparado com outras formas conhecidas de dispensação. Tem sua própria energia para sua operação. Essa energia permite, com sua liberação progressiva, o uso do produto até que esteja esgotado. Mas se essa energia for liberada espontaneamente e violentamente, pode causar mal e bem para as pessoas. Restos dessa energia permanecem no recipiente (aerossol) mesmo depois de consumo total. E ainda há outra coisa, acontece que os propulsores mais usados são inflamáveis e alguns componentes do concentrado também são inflamáveis.
Por essa razão, o conceito de segurança deve acompanhar todas as etapas. Desde a forma como essa energia é incorporada ao tratamento pós-consumo. E se essa condição for mantida, vai ter um sistema de embalagem que supera com a segurança de o0utros conhecidos.
Índice
1. Enchimento e gaseamento
1.1 Setor de enchimento da APS
1.2 Risco de explosão
1.3 Controle de inflamabilidade
1.4 Principal fator do risco na área
1.5 Normas internacionais para instalações elétricas 1.6 Detecção do PhC
1.7 Desenho da planta
1.8 Importância da setorização
1.9 Condições e ações inseguros
1.10 Riscos para o equipe
2. Condicionado
2.1 Setor de depósito do aerossol acabado
2.2 Por que devemos cuidar do armazenamento os aerossóis?
2.3 Como podemos nos proteger?
3. Transporte
3.1 Categorias para o Transporte dos Aerossóis
1. Fase de enchimento e gaseificação
Nesta fase, manipulamos um propulsor inflamável e alguns concentrados que também são inflamáveis e, portanto, tem risco de explosões, incêndios e perigo para os funcionários. Como resultado, todo projeto de planta para a fabricação de aerossóis deve ter um projeto de segurança paralelo anexado para evitar futuras modificações de alto custo.
Muitas vezes encontro com plantas muito bonitas, muito bem desenhadas, mas em que não foi feito um projeto de segurança em paralelo, e quando as construções já estão muito avançadas, perguntaram minha opinião para saber se são seguros. Nestes casos, fui moralmente forçado a dizer a verdade: não são seguros; portanto, adaptações são geralmente necessárias para poder levá-las apenas a uma condição de segurança mínima com um custo determinado, o que poderia ter sido evitado se as instâncias de segurança tivessem sido levadas em conta desde o início.
Nesta parte do processo é essencial destacar a questão da inflamabilidade da APS (Hydrocarbon Propelente), que precisa de certos meios de controle em áreas-chave, assim como o projeto de engenharia adequado que deve estar sempre sujeito a normas (para evitar instalações precárias e improvisadas como tem sido visto muitas vezes).
Outros pontos importantes são o estudo cuidadoso da sucção e ventilação, bem como o controle das fontes de ignição, especialmente aquelas geradas por riscos elétricos.
Tudo isso deve ser feito para evitar misturas inflamáveis ou explosivas no ambiente, além de fontes descontroladas de ignição, tudo deve ser feito para alcançar uma área segura mesmo em condições extremas. Ou seja, a planta deve estar sempre seguro, sem importar o que aconteça.
Por exemplo, se uma mangueira de alta pressão colapsar e um ambiente de gás for inundado, os prejudicados ainda devem ser reduzidos e os riscos devem permanecer sob controle. Essa filosofia é aquela que deve prevalecer quando a tarefa preliminar do projeto de segurança industrial é realizada.
1.1 Setor de enchimento da APS
O setor de enchimento da APS é o risco mais importante na planta, pois é aí que o gás propulsor é manuseado. Estatisticamente, porém, teve mais acidentes ocorridos em outros lugares da fábrica que não estavam exatamente no enchimento da APS, e onde também são manuseados produtos perigosos.
Por exemplo: Se eu uso álcool etílico na minha planta, então eu tenho que considerar as normas de segurança para garantir que não ocorra qualquer acidente para cometer erros com álcool etílico que é um produto inflamável, e obviamente perigoso, e talvez esse seja o perigo mais grave que tenho. Mas se eu também tenho APS, agora é o que representa o maior perigo acima do álcool etílico. Então buscamos cuidar das duas áreas, mas sempre considerando que existem ações perigosas, que podem ser feitas no setor de álcool etílico, ou seja, somos mais permissivos nesse setor, mas não estamos no setor do APS. Se uma reivindicação for encontrada na área onde o álcool etílico é manipulado, ela pode se espalhar para o setor de APS e causar uma reivindicação de grandes proporções.
Para entender a importância da segurança na área da APS é necessário explicar algumas das características desse propulsor, que fazem ser muito perigosa. A APS é mais pesada que o ar, por isso tende a se acumular na parte inferior do local, é sem cor ou sem cheiro. Não é possível cheirá-lo ou vê- lo, a pequena nuvem branca vista nas cabeças de enchimento é simplesmente umidade do ar que se condensa quando a APS se expande.
A APS não é tóxica apenas sufocante, então se sua presença no ar afeta 21% do oxigênio do ar que precisamos para viver, então se afeta, mas não como um tóxico, ao contrário do metano, que é tóxico. Isso significa que se na nossa casa temos gás natural e nos queremos matar e deixar a cozinha aberta vamos conseguir fazer isso acontecer, mas se tivermos gás embalado, butano/propano só teremos uma grande tontura.
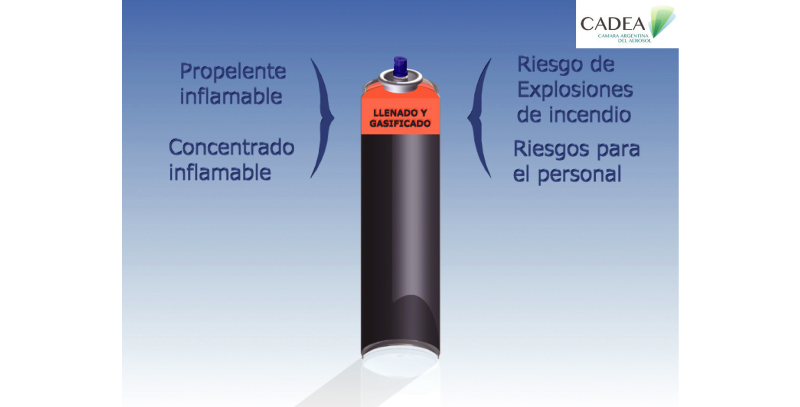
1.2 Risco de explosão
O principal risco característico da APS é sua inflamabilidade. Nesse sentido, é relevante falar sobre dois conceitos vinculados:
1. Sua grande carga de fogo, isso significa que a APS é capaz de produzir muito fogo e calor, então, para diminuir essa carga de fogo precisamos de grande potencial na unidade de extinção do agente extintor que está disponível.
2. Outro conceito importante em relação à APS é o limite inferior e superior da explosividade, há aqueles que também o chamam de limite inferior ou superior de inflamabilidade. A diferença entre esses dois termos, inflamabilidade e explosibilidade, tem a ver com a velocidade de avanço da frente de chama.
O que isso significa a partir do avanço da frente de chama, se você tem um tubo de onde a APS sai, e ele fica inflamado, teremos uma chama como a de um isqueiro, onde você verá diferentes zonas de combustão, áreas muito ricas em combustível dentro e pobres em oxigênio, então você verá outra área onde há muito oxigênio e pouco combustível. Isso é uma inflamação.
Agora, se em um lugar permitimos o vazamento da APS sem ligar, até chegar ao grau de inflamável e aplicamos uma fonte de ignição, a expansão dos gases produzidos pela combustão é instantânea e há um grande aumento de pressão. Isso é o que causa uma explosão e é a diferença entre os dois conceitos.
Para o propano temos um limite menor de 2.4% de gás no ar. Abaixo dessa proporção a mistura é muito baixa em combustível, portanto não teremos combustão, e acima de 9.5% é muito rica, portanto, fora dessa faixa também não teremos combustão. Agora que se dentro da faixa inflamável uma fonte de ignição emergiu, há uma explosão por inflamação.
1.3 Controle da inflamabilidade
Mas se você não pode falar sobre a inflamabilidade da APS se você não estabelecer os meios para o seu controle. Nesse sentido, as instalações devem ser adequadas e realizadas sob as normas existentes, para a concepção e construção das instalações. Acima de tudo, a planta deve ser projetada com a distribuição de tubos, a localização e construção de tanques e a instalação de bombas, todas completamente seguro e padronizado. Todos os acessórios correspondentes às instalações de gás liquefeito também devem ser definidos e distintos. Além disso, deve-se garantir boa sucção e ventilação eficiente, bem como os riscos elétricos gerados por instalações elétricas ineficientes. Juntos, teremos que controlar as misturas inflamáveis e controlar absolutamente todas as fontes de ignição, sobretudo, uma área segura mesmo em condições extremas, pois é um setor onde a APS é preenchida e deve ser seguro mesmo em condições extremas.
Este é um esquema de uma instalação de distribuição de propelentes de hidrocarbonetos para a planta de produção de aerossol com todos os elementos de segurança que é necessário estar incorporados.
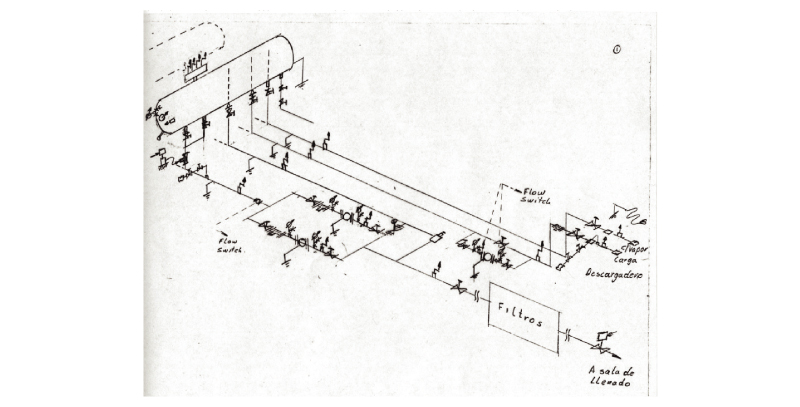
Esta é parte dessa instalação onde você vê as bombas de encanamento instalações elétricas e assim por diante para o sistema de propelente de hidrocarbonetos para a planta de gaseificação.
1.4 Principal fator de risco na área
Os principais fatores de risco na área são as fontes de ignição causadas principalmente pelos riscos proporcionados pelas instalações elétricas. Se entende como ignição como a energia mínima necessária para inflamar uma mistura inflamável ou explosiva.
Existem três conceitos que aumentam o efeito das fontes de ignição:
• Aumento do índice de oxigênio • Aumento da pressão
• Aumento da temperatura
Destes três estamos particularmente interessados no último, pois os aerossóis são fabricados em países frios e quentes, por isso devemos tomar certas precauções especiais, não só pela APS, mas também por solventes, já que seus vapores são facilmente inflamáveis quando há um aumento da temperatura ambiente.
Quando se fala em ignição, você deve ter o controle de várias fontes que produzem nisso, tais como: indução, faíscas eletrostáticas, faíscas de atrito e impacto, aquecimento aerodinâmico de gás ou arcos voltaicos (curtos circuitos).
As fontes consideradas muito perigosas são incêndios abertos, soldas, chamas piloto, escapamentos e ignição automotiva. O controle das fontes de ignição envolve essencialmente o gerenciamento de riscos elétricos através de instalações elétricas apropriado sob padrões.
1.5 Normas internacionais de instalações elétricas
As Normas Americanas para Instalações Elétricas, o Código Elétrico Nacional/NEC, que tem várias classes, sempre foram utilizadas na América Latina, mas a que nos corresponde é a Classe I que define atmosferas explosivas formadas por misturas de gás e que indica dois tipos de divisões:
1) Divisão I: atmosferas explosivas presentes normalmente durante o processo. Um exemplo dessa divisão é o vazamento sistemático da APS que é produzido quando a cabeça de gás na máquina de enchimento sobe. Na pequena câmara ao redor do atuador ou da haste da válvula permanece uma quantidade mínima de gás que é liberada nesta operação e transferida para o ambiente da sala de enchimento.
2) Divisão II: atmosferas explosivas presentes por ruptura anormal ou quebra de equipamento. Essas divisões distinguem quatro grupos de atmosferas explosivas: A (acetileno), B (hidrogênio), C (etileno), D (metano e butano, etc.) sendo o último grupo aplicado à indústria aerossol.
Só para apontá-los, existe a Classe II (atmosferas explosivas, poeiras) e a Classe III (fibras). Também tem outras normas que são europeias (IEC/CENELEC/ EUROPA, adotadas pela Federação Europeia de Aerossol (FEA/Federação Europeia de Aerossol) e pela Associação Britânica para a Fabricação de Aerossol (BAMA/British Association fabricando a fabricação de Aerossol), que em vez de três divisões conta com três tipos de zonas:
• Zona 0 de atmosferas explosivas constantemente presentes
• Zona 1 de atmosferas explosivas presentes intermitentemente durante o processo
• Zona 2 de atmosferas explosivas presentes sob condições anormais ou falha dos equipamentos.
Difere do americano por não falar sobre situações normais ou eventos inesperados, pelo contrário, refere-se à quantidade de tempo em que essas atmosferas inflamáveis estão presentes. Por exemplo, na Zona 0 mais de mil horas por ano, na Zona1entre10e1000enazona2entre0.1e10 horas por ano.
Os materiais elétricos utilizados durante as diferentes zonas são: na Zona 0 é anti-explosivo (expresso por E Ex d). Equipamentos antiexplosivos são recipientes elétricos que cobrem todos os aparelhos e dispositivos não só para evitar que gases entrem no aparelho que possam entrar em contato com condutores ativos, mas também, em caso de explosão interna, o dispositivo resiste a sem entrar em colapso.
A Zona 1 pode usar o critério anti-explosivo, bem como a segurança intrínseca (identificada pela sigla E Ex ia ou ib). A Zona 2 aplica segurança aumentada que o conceito corresponde a: stanco, pressurização, encapsulamento, banho de óleo, etc. (As siglas correspondentes são E Ex o, p, q, m, e).
Diferentes graus de proteção elétrica são permitidos no processamento e gaseificação de aerossóis de acordo com a área em questão.
Abaixo está uma pequena classificação de áreas na planta de enchimento de aerossol: Entenda que sempre falamos de um setor em torno da fonte de emissão
Área do tanque de GLP Zona 0
Descargadero Zona 0
Zona de bomba de GLP Zona 0
Romm gassing (GLP) Zona 0-1
Setor de Condicionamento Geral Zona 2
a) Colocação de atuadores Zona 1
b) Banho de teste Zona 1
c) Túnel de encolhimento térmico Zona 1
1.6 Detecção de PhC
A APS usado para aerossóis é desodorizado não tem cheiro nem da para ver, portanto é necessário mostrar sua presença através de dispositivos de detecção específicos. Por isso, é aconselhável implementar detectores de gás em diversos lugares da planta como o descarregamento, na área do tanque ou na área da bomba, na sala de enchimento e no setor de entrada dos Aerossóis no setor de condicionamento. Recomenda-se detectores e ventilação de emergência adicionais, bem como alarme de luz e som nesses setores.
Outro ponto importante é que tudo o que é feito no setor de processamento de aerossol e, mais especificamente, na área de gaseificação deve ser planejado com antecedência. É dizer, tudo é feito após procedimentos escritos, nada é improvisado. E deve ter registros certificando sua aplicação.