Seguridad en plantas de aerosoles parte I
En toda la vida del aerosol, desde que nace hasta llegar al producto final, interviene el concepto de la seguridad particularmente durante la elaboración. Esta seguridad tiene mucha importancia en el llenado, gasificado y acondicionamiento; así como también en todas tareas que se realizan sobre el Aerosol, sin incluir el gasificado, como ser el almacenado de los aerosoles, las distintas etapas del transporte y todo lo referente al acopio en los centros de distribución y puntos de venta. También el uso por parte del consumidor y finalmente tratamiento post consumo.
¿Por qué hablar de la seguridad en todas estas etapas? El sistema aerosol tiene una particularidad si lo comparamos con otras formas de dispensado conocido. Posee energía propia para su funcionamiento. Esta energía es la que permite, con su liberación progresiva, la utilización del producto hasta agotarlo. Pero si esta energía se libera en forma espontánea y violenta, puede llegar a provocar daños a bienes y a personas. Restos de esta energía permanecen en el envase (aerosol) aún luego de que el mismo ha sido totalmente consumido. Y aún hay algo más, resulta que los propelentes más usados son inflamables y algunos componentes del concentrado también lo son.
Por este motivo el concepto de seguridad debe acompañar todas las etapas. Desde la manera en que se incorpora esta energía hasta el tratamiento post consumo. Y si esta condición se mantiene se obtiene un sistema de empaque que supera en seguridad a otros conocidos.
Índice
1. Llenado y gasificado
1.1 Sector del llenado de PHC
1.2 Riesgo de explosión
1.3 Control de la inflamabilidad
1.4 Principal factor de riesgo en el área
1.5 Normas internacionales de instalaciones eléctricas
1.6 Detección de PHC
1.7 Diseño de planta
1.8 Importancia de la sectorización
1.9 Condiciones y acciones inseguras
1.10 Riesgos para el Personal
2. Acondicionamiento
2.1 Sector depósito de Aerosoles terminados 2.2 ¿Por qué debemos ocuparnos del almacenamiento de los aerosoles?
2.3 ¿Cómo nos podemos proteger?
3. Transporte
3.1 Categorías para el Transporte de Aerosoles
1. Etapa de llenado y gasificado
En esta etapa manipulamos un propelente inflamable y algunos concentrados que también lo son, y, por lo tanto, hay riesgo de explosiones, incendios y peligro para el personal. Debido a ello, todo proyecto de planta para la fabricación de aerosoles debe tener adjunto un proyecto paralelo de seguridad para evitar futuras modificaciones de elevado costo.
Muchas veces me he encontrado con plantas muy bonitas, muy bien diseñadas, pero en las que no se la ha hecho un proyecto de seguridad en paralelo, y cuando ya están muy avanzadas las construcciones, me han preguntado mi parecer acerca de si son seguras. En estos casos, me he visto moralmente obligado a decir la verdad: no son seguras; por lo que generalmente son necesarias adaptaciones para poder llevarlas apenas a una condición mínima de seguridad con un determinado costo, el cual se podría haber evitado si desde el principio se hubieran tomado en cuenta las instancias de seguridad.
En esta parte del proceso es fundamental destacar el tema de la inflamabilidad del PHC (Propelente Hidrocarburo), el cual necesita de ciertos medios de control en áreas claves, como lo es el adecuado diseño de ingeniería que debe estar siempre sujeto a normas (para evitar instalaciones precarias e improvisadas como muchas veces se ha visto).
Otros puntos importantes son el estudio cuidadoso de la aspiración y ventilación, así como el control de fuentes de ignición, especialmente las generadas por riesgos eléctricos.
Todo esto debe hacerse para evitar mezclas inflamables o explosivas en el ambiente, además de fuentes de ignición descontroladas, Todo debe hacerse para lograr un área segura aún en condiciones extremas. Esto es, la planta debe ser siempre segura pase lo que pase.
Por ejemplo, si se colapsa una manguera de alta presión y se inunda un ambiente de gas, aun así, los daños deben ser reducidos y los riesgos deben permanecer bajo control. Esta filosofía, es la que debe prevalecer cuando se efectúa la tarea preliminar del diseño de seguridad Industrial.
1.1 Sector del llenado de PHC
El sector del llenado de PHC es el riesgo más importante que hay en la planta, porque es ahí donde se manipula el gas propelente. Sin embargo, estadísticamente se han registrado más siniestros que se produjeron en otros lugares de la planta que no fue precisamente en el llenado de PHC, y donde también se manipulan productos peligrosos.
Por ejemplo: Si en mi planta empleo alcohol etílico, entonces, tengo que considerar las normas de seguridad para cuidar que no ocurra cualquier percance por cometer errores con el alcohol etílico que es un producto inflamable, y evidentemente peligroso, y quizá ese es el peligro más grave que tengo. Pero si además tengo PHC, es ahora el que representa el mayor peligro por encima del alcohol etílico. Entonces se procura cuidar ambas áreas, pero siempre considerando que hay acciones peligrosas, que se pueden hacer en el sector del alcohol etílico, es decir somos más permisivos en este sector, pero no lo somos en el del PHC. Si se llegara a tener un siniestro en la zona donde se manipula el alcohol etílico, eso puede llegar a propagarse al sector del PHC y causar un siniestro de grandes proporciones.
Para comprender la importancia de la seguridad en la zona del PHC es necesario explicar algunas de las características de este propelente, que lo hacen muy peligroso. El PHC es más pesado que el aire por eso tiende a acumularse en la parte baja de los locales, es incoloro e inodoro. No es posible olerlo ni verlo, esa pequeña nube blanca que se ve en los cabezales de las llenadoras es simplemente humedad del aire que se condensa al momento que se expande el PHC.
El PHC no es tóxico solo es asfixiante, o sea que, si su presencia en el aire llega a afectar al 21% del oxígeno del aire que necesitamos para vivir, entonces si afecta, pero no como un tóxico, a diferencia del metano, el cual es tóxico. Esto quiere decir que si en nuestra casa tenemos gas natural y nos queremos suicidar y dejamos la cocina abierta lo vamos a lograr, pero si tenemos gas envasado, butano/propano solo obtendremos un gran mareo.
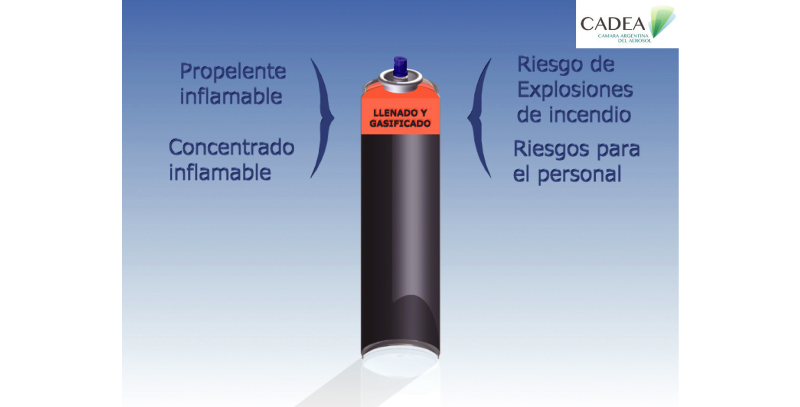
1.2 Riesgo de explosión
La principal característica de riesgo del PHC es su inflamabilidad. Al respecto es pertinente hablar sobre dos conceptos vinculados:
1. Su gran carga de fuego, esto quiere decir que el PHC es capaz de producir mucho fuego y calor, por lo que, para disminuir esa carga de fuego necesitamos un gran potencial en unidad de extinción del agente extintor que se tenga.
2. Otro concepto importante con respecto al PHC es el límite inferior y superior de explosividad, hay quienes lo llaman también el límite inferior o superior de inflamabilidad. La diferencia entre estos dos términos, inflamabilidad y explosibilidad, tiene que ver con la velocidad de avance del frente de llama.
Qué significa esto del avance del frente de llama, si se tiene un tubo del cual sale PHC, y se inflama, vamos a tener una llama como la de un mechero, donde van a ver distintas zonas de combustión, zonas muy ricas en el combustible en la parte interior y pobres en oxígeno, luego se va a ver otra zona donde hay mucho oxígeno y poco combustible. Eso es una inflamación.
Ahora, si en un local permitimos la fuga de PHC sin encenderse, hasta llegar al grado de inflamable y aplicamos una fuente de ignición, la expansión de los gases producidos por la combustión es instantánea y hay un gran aumento de la presión. Eso es lo que produce una explosión y es la diferencia entre los dos conceptos.
Para el propano tenemos un límite inferior de 2,4% de gas en aire. Por debajo de esa proporción la mezcla es muy pobre en combustible, por lo tanto, no vamos a tener combustión, y por encima de 9,5% es demasiado rica, por lo tanto, fuera de ese rango tampoco vamos a tener combustión. Ahora que si dentro del rango de inflamable surgiera una fuente de ignición se tienen una explosión por inflamación.
1.3 Control de la inflamabilidad
Pero no se puede hablar de inflamabilidad del PHC si no se establecen los medios para su control. En este sentido las instalaciones deben ser las adecuadas y realizadas bajo las normas existentes, para el diseño y la construcción de las instalaciones. Sobre todo, la planta debe ser diseñada pensando en la distribución de las cañerías, la ubicación y construcción de tanques y la instalación de bombas, todo completamente seguro y normalizado. También se debe definir y distinguir todos los accesorios que corresponden a las instalaciones del gas licuado. Además, se debe garantizar una buena aspiración y una eficiente ventilación, además de controlar los riesgos eléctricos que son los que se generan por ineficientes instalaciones eléctricas. Aunado, habrá que controlar las mezclas inflamables y controlar absolutamente todas las fuentes de ignición y, sobre todo, conseguir un área que sea segura aún en condiciones extremas, porque es un sector donde se llena PHC debe ser seguro aún en condiciones extremas.
Este es un esquema de una instalación de distribución de propelente hidrocarburo a planta de producción de aerosoles con todos los elementos de seguridad qué necesitan están incorporados.
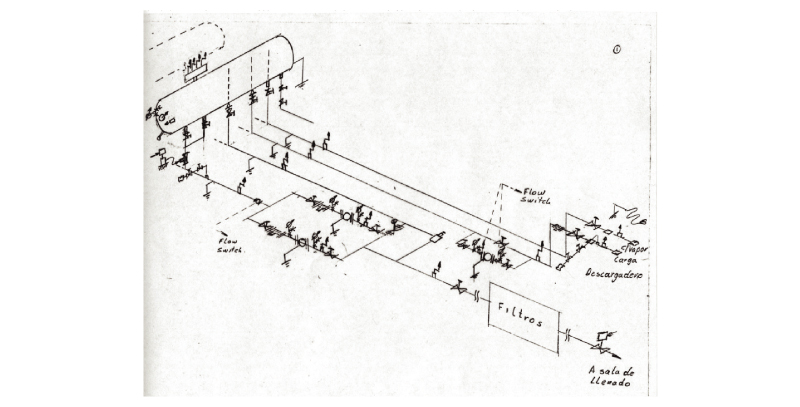
Esta es parte de esa instalación donde se ven las bombas cañerías instalaciones eléctricas y demás para el sistema de propelente hidrocarburo a la planta de gasificado.
1.4 Principal factor de riesgo en el área
Los principales factores de riesgo del área son las fuentes de ignición provocadas principalmente por los riesgos aportados por las instalaciones eléctricas. Se entiende como ignición como la mínima energía necesaria para encender una mezcla inflamable o explosiva.
Hay tres conceptos que potencian el efecto de las fuentes de ignición:
• Aumento del índice de oxígeno • Aumento de la presión
• Aumento de la temperatura
De estos tres el que nos interesa especialmente es el último, porque los aerosoles se fabrican en países tanto fríos como cálidos, debido a ello hay que tener ciertas precauciones especiales, no solo por el PHC, sino también por los solventes, ya que sus vapores son fácilmente inflamables cuando se produce un aumento de la temperatura ambiente.
Cuando se habla de ignición, se debe tener control de varias fuentes que la producen tales como: la inducción, las chispas electrostáticas, las chispas de fricción e impacto, el calentamiento aerodinámico de gases o los arcos voltaicos (cortocircuitos).
Las fuentes consideradas muy peligrosas son los fuegos abiertos, soldaduras, llamas piloto, escapes y encendido de automotores. El control de las fuentes de ignición implica fundamentalmente el manejo de los riesgos eléctricos por medio de instalaciones eléctricas adecuadas bajo normas.
1.5 Normas internacionales de instalaciones eléctricas
Desde hace mucho tiempo siempre se han empleado en América Latina las Normas para instalaciones eléctricas de los EEUU, el Código Nacional de Electricidad (National Electrical Code/NEC), que cuenta con varias clases, pero la que nos corresponde a nosotros es la Clase I que define las atmósferas explosivas formadas por mezclas de gases y donde se indica dos tipos de divisiones:
1) División I: atmósferas explosivas presentes en forma normal durante el proceso. Un ejemplo de esta división es la fuga sistemática de PHC que se produce cuando el cabezal de gasificado en la máquina llenadora sube. En la pequeña cámara que rodea el actuador o el vástago de la válvula permanece una mínima cantidad de gas que se libera en esta operación y es transferida al ambiente de la sala de llenado.
2) División II: atmósferas explosivas presentes por rotura o avería de los equipos en forma anormal. En estas divisiones se distinguen cuatro grupos de atmósferas explosivas: A (acetileno), B (hidrogeno), C (etileno), D (metano y butano, etc.) siendo el último grupo el que aplica a la industria de aerosol.
Solo por señalarlas, existen la Clase II (atmósferas explosivas, polvos) y la Clase III (fibras). También hay otras normas que son las europeas (IEC/CENELEC/EUROPA, adoptadas por Federation European of Aerosol (FEA/ Federación Europea del Aerosol) y por la Asociación Británica de Manufactura de Aerosoles (BAMA/British Asociation Manufactury of Aerosol), que en lugar de tres divisiones cuenta con tres tipos de zonas:
• La Zona 0 de atmósferas explosivas presentes en forma constante
• La Zona 1 de atmósferas explosivas presentes en forma intermitente durante el proceso
• La Zona 2 de atmósferas explosivas presentes bajo condiciones anormales o falla de los equipos.
Difiere de la americana al no hablar de situaciones normales o eventos inesperados, por el contrario, hace referencia a la cantidad de tiempo en el cual estas atmósferas inflamables están presentes. Por ejemplo, en la Zona 0 más de mil horas al año, en la Zona 1 entre 10 y 1000 y en la zona 2 entre 0.1 y 10 horas al año.
Los materiales eléctricos empleados durante las distintas zonas son: en la Zona 0 es antiexplosivo (expresado por siglas E Ex d). Los equipos antiexplosivos son receptáculos eléctricos que cubren todos los aparatos y dispositivos no solo para impedir el ingreso de gases al interior del artefacto que pueden entrar en contacto con conductores activos, sino que, además, en caso de producirse una explosión interna, el dispositivo lo resiste sin colapsarse.
En una Zona 1 se puede utilizar el criterio antiexplosivo y también de seguridad intrínseca (se identifica por las siglas E Ex ia o ib). En la Zona 2 se aplica seguridad aumentada que concepto que corresponde a: estanco, presurización, encapsulado, baño de aceite, etc. (Las siglas que corresponden son E Ex o, p, q, m, e).
En la elaboración y el gasificado de los Aerosoles se permiten distintos grados de protección eléctrica de acuerdo con el área que se trate.
A continuación, se presenta una pequeña clasificación de zonas en la planta de llenado de aerosoles: Entiéndase que siempre hablamos de un sector que rodea a la fuente de emisión
Zona de tanques de GLP Zona 0
Descargadero Zona 0
Zona de bombas de GLP Zona 0
Gassing romm (GLP) Zona 0-1
Sector de acondicionado General Zona 2
a) Colocación de los actuadores Zona 1
b) Baño de prueba Zona 1
c) Túnel termacontracción Zona 1
1.6 Detección de PHC
El PHC que se emplea para aerosoles está desodorizado no se huele ni se ve, por consiguiente, es necesario evidenciar su presencia por medio de dispositivos de detección específicos. Por eso se aconseja la implementación de detectores de gas en diversos lugares de la planta como el descargadero, en la zona de tanques o en la de bombas, en la sala de llenado y en el sector de entrada de los Aerosoles alsectordeacondicionado.Seaconsejandetectores y ventilación adicional emergencia, además de alarma lumínica y sonora en esos sectores.
Otro punto importante es que todo lo que se hace en el sector de elaboración de aerosoles y más específicamente en el área de gasificado debe planificarse previamente. Es decir, todo se hace siguiendo procedimientos escritos, nada se improvisa. Y debe haber registros que certifiquen su aplicación.